Wool spinning carding system capable of automatically controlling feeding
A feeding and hair roller technology, applied in fiber processing, deburring devices, textiles and papermaking, etc., can solve the problems of unfavorable continuous production, high labor cost, high labor intensity, etc., to improve accuracy and continuous The effect of production, improving efficiency and sliver uniformity, and improving conveying efficiency
- Summary
- Abstract
- Description
- Claims
- Application Information
AI Technical Summary
Problems solved by technology
Method used
Image
Examples
Embodiment Construction
[0022] The present invention is described in detail below in conjunction with accompanying drawing:
[0023] combine Figure 1 to Figure 5 , a wool spinning carding system that automatically controls feeding, including a wool blending machine 1, a cotton feeding fan 2, and a two-way cotton distribution device group. 17 is connected with the air inlet end of the cotton blower 2, and the raw materials after the pre-opening are transported. The wool closing machine 1 comprises a wool feeding curtain 11, a breast cylinder 12 and a first doffer 13, and the wool feeding curtain 11, a breast cylinder 12 and the first doffer 13 are arranged sequentially from back to front. A wool feeding roller group 14 is arranged between the wool feeding curtain 11 and the chest cylinder 12. The wool feeding roller group 14 adopts a double wool feeding roller structure, and is specifically composed of an upper wool feeding roller and a lower wool feeding roller. The top of the breast cylinder 12 i...
PUM
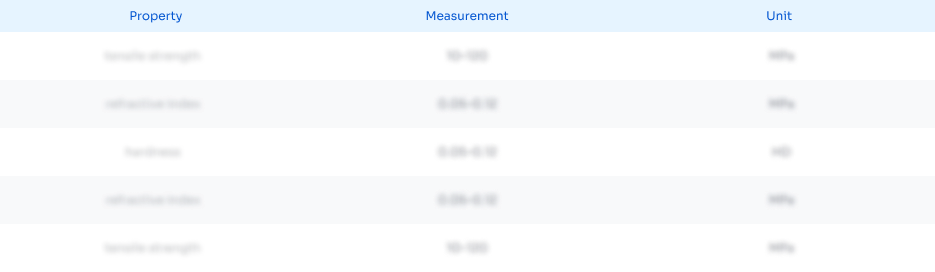
Abstract
Description
Claims
Application Information

- R&D Engineer
- R&D Manager
- IP Professional
- Industry Leading Data Capabilities
- Powerful AI technology
- Patent DNA Extraction
Browse by: Latest US Patents, China's latest patents, Technical Efficacy Thesaurus, Application Domain, Technology Topic, Popular Technical Reports.
© 2024 PatSnap. All rights reserved.Legal|Privacy policy|Modern Slavery Act Transparency Statement|Sitemap|About US| Contact US: help@patsnap.com