A track changing vehicle
A technology for working vehicles and rails, which is applied in the directions of track, track laying, track maintenance, etc. It can solve problems such as rail invasion, hidden dangers of train operation safety, long rail movement, etc., to reduce stress, save time for unloading new rails, reduce The effect of the time of collision and up-track
- Summary
- Abstract
- Description
- Claims
- Application Information
AI Technical Summary
Problems solved by technology
Method used
Image
Examples
Embodiment 1
[0039] as attached figure 1 And attached figure 2 As shown, a specific embodiment of a rail changing operation vehicle. The rail changing operation vehicle 1 includes: a replacement module 3 , a loading and unloading module 4 and a transportation module 5 which are sequentially connected along the construction work direction. When changing the new rail 6, the operation direction of the rail change vehicle 1 is as attached figure 1 Shown in the middle arrow L1, the operation direction of the rail change vehicle 1 when reclaiming the old rail 10 is as attached figure 2 Indicated by the middle arrow L2. in:
[0040] The transport module 5 loads and transports the new rail 6 .
[0041] The loading and unloading module 4 is provided with a rail transfer device 7 , and the rail transfer device 7 transfers the new rail 6 to the replacement module 3 .
[0042] The loading and unloading module 4 is provided with a rail splitting device 8, and the rail splitting device 8 adjusts ...
Embodiment 2
[0059] In this embodiment, the rail change vehicle 1 also includes a rail welding module 2 connected to the replacement module 3 and capable of operating independently for welding the new rails 6 adjacent to each other on the line. The rail welding module 2 has a self-propelled power. When the rail changing vehicle 1 reaches the construction starting point within the skylight time, the rail welding module 2 is unlocked and decoupled from the rail changing vehicle 1 . After the replacement module 3 unloads the new rail 6 delivered into the sinker groove of the sleeper, the rail welding module 2 welds the new rails 6 adjacent to each other on the line. as attached Figure 5 As shown, the rail changing operation vehicle 1 includes: a welding rail module 2, a replacement module 3, a loading and unloading module 4 and a transport module 5, which are sequentially connected along the construction operation direction, and the operation method includes the following steps:
[0060] S...
Embodiment 3
[0068] In this embodiment, the rail changing operation vehicle 1 also includes a dismantling module 11 connected between the replacement module 3 and the loading and unloading module 4. After the rail dividing device 8 adjusts the new rails 6 transferred to a suitable distance, the dismantling module 11 Remove the remaining fasteners from the line. as attached Image 6 As shown, the track changing operation vehicle 1 includes: a replacement module 3, a disassembly module 11, a loading and unloading module 4 and a transport module 5, which are sequentially connected along the construction operation direction, and the operation method includes the following steps:
[0069] S11: After the rail fasteners are disassembled according to the mode of tightening 1 loosening 8, the rail change vehicle 1 arrives at the construction starting point within the skylight time, and the new rail 6 is loaded and transported by the transport module 5;
[0070] S12: The rail transfer device 7 arra...
PUM
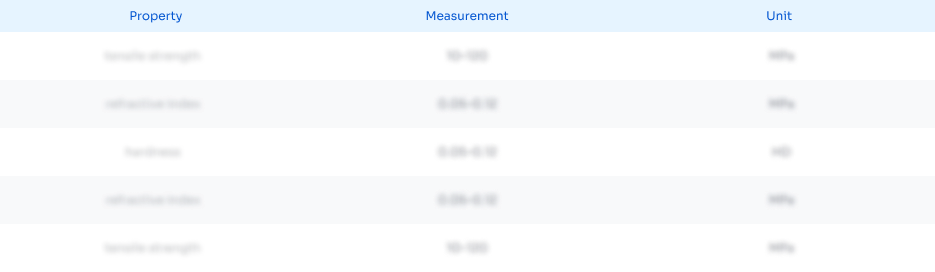
Abstract
Description
Claims
Application Information

- R&D
- Intellectual Property
- Life Sciences
- Materials
- Tech Scout
- Unparalleled Data Quality
- Higher Quality Content
- 60% Fewer Hallucinations
Browse by: Latest US Patents, China's latest patents, Technical Efficacy Thesaurus, Application Domain, Technology Topic, Popular Technical Reports.
© 2025 PatSnap. All rights reserved.Legal|Privacy policy|Modern Slavery Act Transparency Statement|Sitemap|About US| Contact US: help@patsnap.com