Assembly structure and method of an anisotropic large dynamic fringe image transformation tube
An anisotropic and assembly structure technology, applied in the field of assembly of ultra-fast diagnostic optoelectronic devices, can solve the problem of difficulty in controlling the inclination angle between the space electrode and the electron optical system axis, easily destroying the symmetry of the electron optical system, and the decrease in spatial resolution in the scanning direction, etc. problems, to achieve good assembly accuracy and consistency, save manpower and material resources, and to achieve the effect of solid and reliable fusion sealing
- Summary
- Abstract
- Description
- Claims
- Application Information
AI Technical Summary
Problems solved by technology
Method used
Image
Examples
Embodiment Construction
[0057] According to the electrode structure of the stripe image transformation tube, the present invention forms parts with similar structures, materials and processes into a part family (group), and assembles according to the process of the part family. The group modularization method in the assembly process is to use the similarity of the parts in the electrode system and classify them into groups according to certain criteria. Products in the same group can be processed in the same way, thereby expanding the batch size and reducing the assembly process. The method is more efficient , improved efficiency.
[0058] The time pre-focus electrode system and the time focus electrode system in the anisotropic focusing stripe image transformation tube are basically similar in structure, and the space electrode system is composed of four arc-surface electrodes with the same structure, which meet the conditions of group assembly. Therefore, In the assembly of the striped tube electro...
PUM
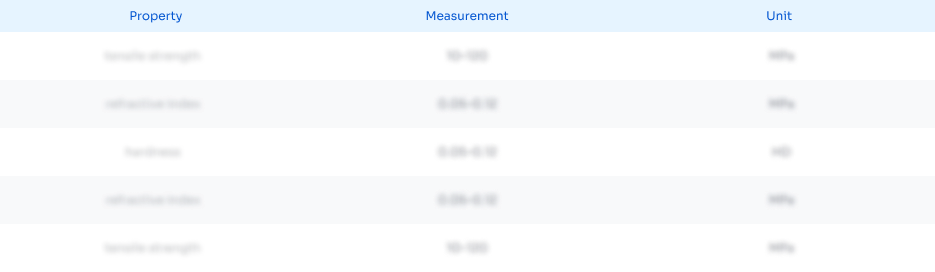
Abstract
Description
Claims
Application Information

- R&D Engineer
- R&D Manager
- IP Professional
- Industry Leading Data Capabilities
- Powerful AI technology
- Patent DNA Extraction
Browse by: Latest US Patents, China's latest patents, Technical Efficacy Thesaurus, Application Domain, Technology Topic, Popular Technical Reports.
© 2024 PatSnap. All rights reserved.Legal|Privacy policy|Modern Slavery Act Transparency Statement|Sitemap|About US| Contact US: help@patsnap.com