A kind of midsole plate for shoes and its preparation method
A technology for soleplates and shoes, which is applied in the direction of textiles and papermaking, papermaking, reinforcing agent addition, etc. It can solve the problems of reduced plasticity, reduced folding resistance of finished products, and reduced swelling ability, and achieves good punching and durability. Wear it and realize the effect of recycling
- Summary
- Abstract
- Description
- Claims
- Application Information
AI Technical Summary
Problems solved by technology
Method used
Image
Examples
preparation example Construction
[0016] A method for preparing midsole boards for shoes, comprising mixing 45-55 parts by weight of fiber pulp and 45-55 parts by weight of bleached kraft wood pulp, and adjusting the mixed pulp to an online concentration of 2.5-3.5 wt%. After the first press, add 0.5-1 parts by weight of dry strength agent for pre-impregnation, and then perform the second press to adjust the pulp after the second press. The dryness of the material is 45-50%, and then the slurry is impregnated, and after the impregnation, the third pressing process is performed to obtain a board, and the glue absorption amount of the board is 30-40% of the mixed slurry. %.
[0017] As can be seen from the foregoing description, the beneficial effects of the present invention are:
[0018] (1) Add fiber pulp raw materials to bleached kraft wood pulp. Fiber pulp can be obtained from waste cardboard, thereby partially replacing bleached kraft wood pulp as the raw material for midsole boards for shoemaking. It is ...
Embodiment 1
[0040] The preparation method of the midsole plate for shoes of the present embodiment comprises the following steps:
[0041] 1. According to the total mass fraction of 100%, it includes the following components: mix the fiber pulp of waste cardboard and 45% bleached kraft wood pulp accounting for 45% of the total mass fraction, and adjust it into a papermaking pulp with an online concentration of 2.5% ;
[0042] 2. Add a sizing agent (one of dispersed loose glue, AKD, etc.) in the slurry tank, and the dosage is 0.5% for the slurry, and carry out preliminary internal sizing to improve the water resistance;
[0043]3. Add a wet strength agent (one of PPE, cationic polyacrylamide, PAE, melamine formaldehyde resin, etc.) to the head box, and the dosage is 0.5% to the pulp to ensure that the cardboard has a certain wet strength;
[0044] 4. Use a vacuum press roller for the first pressing treatment, pre-impregnate after the first pressing treatment, add a dry strength agent (gua...
Embodiment 2
[0049] The preparation method of the midsole plate for shoes of the present embodiment comprises the following steps:
[0050] 1. According to the total mass fraction of 100%, it includes the following components: mix the fiber pulp of waste cardboard and 45% bleached kraft wood pulp accounting for 55% of the total mass fraction, and adjust it into a papermaking pulp with an online concentration of 3.5%. ;
[0051] 2. Add a sizing agent (one of dispersed loose glue, AKD, etc.) in the slurry tank, and the dosage is 1% for the slurry, and carry out preliminary internal sizing to improve the water resistance;
[0052] 3. Add a wet strength agent (one of PPE, cationic polyacrylamide, PAE, melamine formaldehyde resin, etc.) to the head box, and the dosage is 2% to the pulp to ensure that the cardboard has a certain wet strength;
[0053] 4. Use a vacuum press roller for the first pressing treatment, pre-impregnate after the first pressing treatment, add a dry strength agent (guar ...
PUM
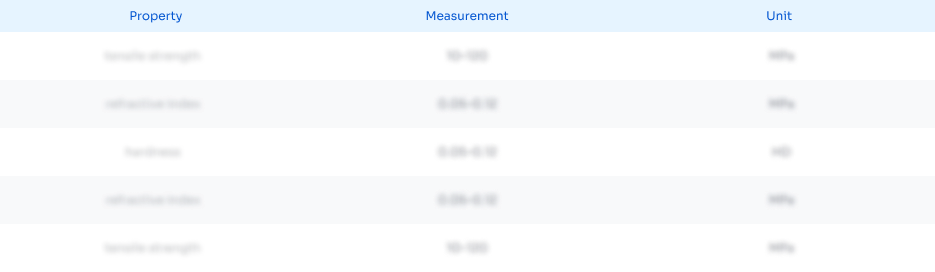
Abstract
Description
Claims
Application Information

- R&D
- Intellectual Property
- Life Sciences
- Materials
- Tech Scout
- Unparalleled Data Quality
- Higher Quality Content
- 60% Fewer Hallucinations
Browse by: Latest US Patents, China's latest patents, Technical Efficacy Thesaurus, Application Domain, Technology Topic, Popular Technical Reports.
© 2025 PatSnap. All rights reserved.Legal|Privacy policy|Modern Slavery Act Transparency Statement|Sitemap|About US| Contact US: help@patsnap.com