Cement grouting mortar with high permeability and preparation method thereof
A high-permeability, cement technology, applied in the field of building materials, can solve the problems of unsatisfactory stability, complicated synthesis process, and increased production cost, and achieve the effects of high fluidity, simple process operation, and economical production cost
- Summary
- Abstract
- Description
- Claims
- Application Information
AI Technical Summary
Problems solved by technology
Method used
Image
Examples
Embodiment 1
[0023] The high-permeability cement pouring mortar involved in this embodiment is made of the following mass proportioning components: P·II 42.5R Portland cement 56.1%; admixture 0.06%; admixture 4.2%; sand 7.64% and Water 32%.
[0024] The preparation method of the above-mentioned high-permeability cement grout of the present embodiment comprises the following steps:
[0025] 1) At 20°C, mix P·Ⅱ42.5R Portland cement with a mass percentage of 56.1%, 0.06% admixture, 4.2% admixture and 7.64% sand by manual or mechanical mixing until basically uniform;
[0026] 2) Use a planetary mortar mixer at a speed of 80r / min for dry mixing for 60s, then gradually add water with a mass percentage of 32% within 30s, keep stirring during the water addition, continue stirring for 120s, and end to obtain perfusion mortar. In this embodiment, the water-cement ratio used is 0.57.
[0027] Its main properties are shown in Table 1.
Embodiment 2
[0029] The high-permeability cement pouring mortar involved in this embodiment is made of the following components in mass ratio: P·II 42.5R Portland cement 51%; admixture 0.08%; admixture 5%; sand 12.5% and Water 31.42%.
[0030] The preparation method of the above-mentioned high-permeability cement grout of the present embodiment comprises the following steps:
[0031] 1) At 0°C, mix P·II42.5R Portland cement with a mass percentage of 51%, 0.08% admixture, 5% admixture and 12.5% sand by manual or mechanical mixing until basically uniform;
[0032] 2) Use a planetary mortar mixer with a speed of 80r / min for dry mixing for 90s, then gradually add water with a mass percentage of 31.42% within 45s, keep stirring during the water addition, continue stirring for 150s, and end to obtain perfusion mortar.
[0033] In this embodiment, the water-cement ratio used is 0.62. Its main properties are shown in Table 1.
Embodiment 3
[0035] The high-permeability cement pouring mortar involved in this embodiment is made of the following mass proportioning components: P·II 42.5R Portland cement 61%; admixture 0.12%; admixture 3%; sand 6.5% and Water 29.38%.
[0036] The preparation method of the above-mentioned high-permeability cement grout of the present embodiment comprises the following steps:
[0037] 1) At 35°C, mix 61% of P·II42.5R Portland cement, 0.12% of admixture, 3% of admixture and 6.5% of sand by manual or mechanical mixing until basically uniform;
[0038] 2) Use a planetary mortar mixer at a speed of 80r / min for dry mixing for 120s, then gradually add water with a mass percentage of 29.38% within 60s, keep stirring during the water addition, continue stirring for 180s, and end to obtain perfusion mortar.
[0039] In this embodiment, the adopted water-cement ratio is 0.48. Its main properties are shown in Table 1.
PUM
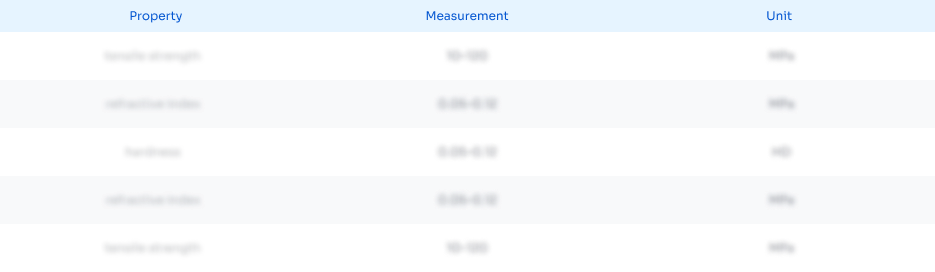
Abstract
Description
Claims
Application Information

- R&D Engineer
- R&D Manager
- IP Professional
- Industry Leading Data Capabilities
- Powerful AI technology
- Patent DNA Extraction
Browse by: Latest US Patents, China's latest patents, Technical Efficacy Thesaurus, Application Domain, Technology Topic, Popular Technical Reports.
© 2024 PatSnap. All rights reserved.Legal|Privacy policy|Modern Slavery Act Transparency Statement|Sitemap|About US| Contact US: help@patsnap.com