Trans-dimension six-freedom-degree automatic butt joint system
An automatic docking and degree of freedom technology, which is applied in the direction of program-controlled manipulators, manufacturing tools, manipulators, etc., can solve the problem that the six-degree-of-freedom docking robot cannot satisfy cross-scale transportation and automatic docking at the same time, and achieve large carrying capacity and accurate and reliable positioning , easy to control the effect
- Summary
- Abstract
- Description
- Claims
- Application Information
AI Technical Summary
Problems solved by technology
Method used
Image
Examples
Embodiment Construction
[0031] The following description serves to disclose the present invention to enable those skilled in the art to carry out the present invention. The preferred embodiments described below are only examples, and those skilled in the art can devise other obvious variations. The basic principles of the present invention defined in the following description can be applied to other embodiments, variations, improvements, equivalents and other technical solutions without departing from the spirit and scope of the present invention.
[0032] Such as Figure 1 to Figure 8 As shown, according to the inventive spirit of the present invention, a cross-scale six-degree-of-freedom automatic docking system is provided, which includes a self-propelled mechanism 1, a level adjustment mechanism 2, a plane adjustment mechanism 3 and a bottom plate 4, wherein the level adjustment mechanism 2 is set on the self-propelled mechanism 1, the plane adjustment mechanism 3 is set on the level adjustment ...
PUM
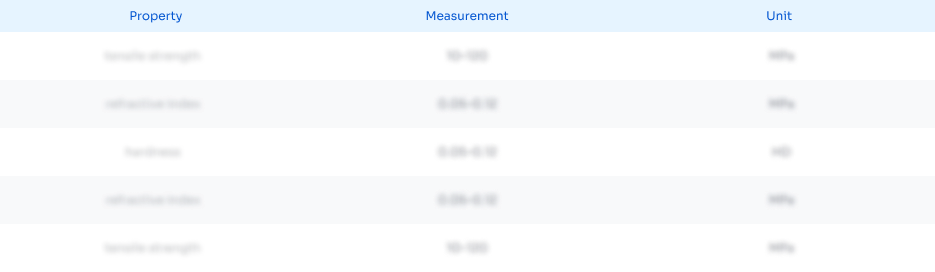
Abstract
Description
Claims
Application Information

- R&D
- Intellectual Property
- Life Sciences
- Materials
- Tech Scout
- Unparalleled Data Quality
- Higher Quality Content
- 60% Fewer Hallucinations
Browse by: Latest US Patents, China's latest patents, Technical Efficacy Thesaurus, Application Domain, Technology Topic, Popular Technical Reports.
© 2025 PatSnap. All rights reserved.Legal|Privacy policy|Modern Slavery Act Transparency Statement|Sitemap|About US| Contact US: help@patsnap.com