Additive for strengthening calcification and roasting of magnetite-type tin-iron tailings and method for separating tin-iron by calcification and roasting of tin-iron tailings
A technology of calcification roasting and magnetite, which is applied in the field of strengthening magnetite-type tin-iron tailings calcification roasting additives, tin-iron tailings roasting additives, and strengthening magnetite-type tin-iron tailings calcification roasting to separate tin and iron. Solve the problems of complex treatment process, difficulty in separation of tin and iron, difficulty in utilization, etc., achieve enhanced roasting effect, low cost, and realize the effect of industrialized production
- Summary
- Abstract
- Description
- Claims
- Application Information
AI Technical Summary
Problems solved by technology
Method used
Examples
Embodiment 1
[0037] Using magnetite-type tin-containing iron tailings with a tin grade of 0.32% and an iron grade of 34.52% as raw materials, after the tin-iron tailings raw materials are dehydrated and dried to a certain moisture content, additives are added according to 25% of the mass fraction (the ratio is Quicklime: dolomite: carbonate type iron-containing tailings: sodium humate = 60%: 10%: 20%: 10%), after mixing the materials evenly, add suitable water to form agglomerates, and finally carry out dehydration and drying; The final agglomerate is put into the roaster, and the volume concentration of CO [CO / (CO+CO 2 )] is 16%, the magnetization roasting temperature is 700°C, and the roasting time is 120min. After the roasting is completed, the agglomerate is cooled with water, ground to 80% less than 0.074mm, and magnetically separated under the condition of a magnetic field strength of 800GS. An iron concentrate with an iron grade of 62.56% (tin grade 0.05%) was obtained, the iron rec...
Embodiment 2
[0039] Using magnetite-type tin-containing iron tailings with a tin grade of 0.32% and an iron grade of 34.52% as raw materials, after the tin-iron tailings raw materials are dehydrated and dried to a certain moisture content, additives are added according to 10% of the mass fraction (the ratio is Quicklime: dolomite: carbonate type iron-containing tailings: sodium humate = 40%: 10%: 40%: 10%), after mixing the materials evenly, add suitable water to form agglomerates, and finally carry out dehydration and drying; The final agglomerate is put into the roaster, and the volume concentration of CO [CO / (CO+CO 2 )] is 3%, the magnetization roasting temperature is 900°C, and the magnetization roasting time is 60min. After the roasting is completed, the agglomerate is cooled with water, ground to 80% less than 0.074mm, and magnetically separated under the condition of a magnetic field strength of 1200GS. An iron concentrate with an iron grade of 61.31% (tin grade 0.06%) was obtained,...
Embodiment 3
[0041] Using magnetite-type tin-containing iron tailings with a tin grade of 0.45% and an iron grade of 45.12% as raw materials, after the tin-iron tailings raw materials are dehydrated and dried to a certain moisture content, additives are added according to 12% of the mass fraction (the ratio is Quicklime: dolomite: carbonate type iron-containing tailings: sodium humate = 40%: 19%: 40%: 1%), after mixing the materials evenly, add suitable water to form agglomerates, and finally carry out dehydration and drying; The final agglomerate is put into the roaster, and the volume concentration of CO [CO / (CO+CO 2 )] is 5%, the magnetization roasting temperature is 700°C, and the magnetization roasting time is 90min. After the roasting is completed, the agglomerate is cooled with water, ground to 80% less than 0.074mm, and magnetically separated under the condition of a magnetic field strength of 1000GS. An iron concentrate with an iron grade of 65.33% (tin grade 0.07%) was obtained, ...
PUM
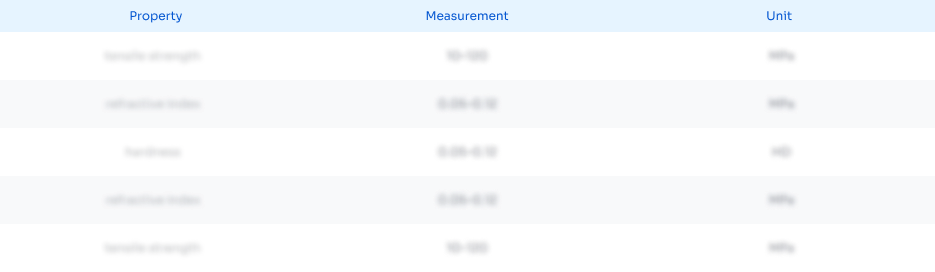
Abstract
Description
Claims
Application Information

- R&D
- Intellectual Property
- Life Sciences
- Materials
- Tech Scout
- Unparalleled Data Quality
- Higher Quality Content
- 60% Fewer Hallucinations
Browse by: Latest US Patents, China's latest patents, Technical Efficacy Thesaurus, Application Domain, Technology Topic, Popular Technical Reports.
© 2025 PatSnap. All rights reserved.Legal|Privacy policy|Modern Slavery Act Transparency Statement|Sitemap|About US| Contact US: help@patsnap.com