Integrated process technology of whitening, shaping and modifying natural powdery quartz
A process technology, quartz technology, applied in the field of modification integrated process, shaping, and natural powder quartz whitening, can solve the problems of high quality modification equipment, high production cost, strict equipment requirements, etc., to improve mechanical processing. Performance and mechanical properties, easy to mass industrial production, significant activation effect
- Summary
- Abstract
- Description
- Claims
- Application Information
AI Technical Summary
Problems solved by technology
Method used
Image
Examples
Embodiment 1
[0036] First, the natural powder quartz ore is manually selected to remove red, yellow, brown and other color impurities, and then it is ground and classified to obtain a 3000-mesh powder (whiteness is 74.2%), and charcoal is added (the amount is 1.5% of the weight of the powder). %) and sodium chloride (the amount is 1% of the weight of the powder) and stir evenly, then send the material into the rotary kiln, calcined at 900°C for 1.5 hours, cool the material, and send it into the high-speed mixer for beating Dispersion (the processing output of the disintegrator is 1 ton / hour), modification. Heat the FT-3 aluminum-titanium composite coupling agent to 100°C for melting, adjust the flow rate of the automatic dosing pump, the flow rate of FT-3 aluminum-titanium composite coupling agent is 20 kg / hour, and the flow rate of silicon 69 is 10 kg / hour, the two active agents are simultaneously sprayed into the dispersing machine barrel for activation treatment to produce high-purity...
Embodiment 2
[0038] First, the natural powder quartz ore is hand-selected to remove red, yellow, brown and other color impurities, ball milled and classified to obtain a powder of 1250 mesh (whiteness 73.8%), and refined coal (amount of 2% of the weight of the powder) is added. %) and sodium carbonate (the amount is 1% of the weight of the powder) and stir evenly, then put the material into a sagger, install it in a kiln (downdraft kiln), and calcinate at 1100°C for 4 hours, cool the material, and Disintegration in the disintegrator (the processing output of the disintegrator is 1.5 tons / hour), modification. Heat the FT-4 aluminum-titanium composite coupling agent to 100°C for melting, adjust the flow rate of the automatic dosing pump, the flow rate of the FT-4 aluminum-titanium composite coupling agent is 15 kg / hour, and the flow rate of the silane coupling agent KH550 At 15 kg / hour, the two active agents are simultaneously sprayed into the dispersion machine barrel for activation treatme...
Embodiment 3
[0040]First, the natural powder quartz ore is hand-selected to remove red, yellow, brown and other color impurities, ball milled and classified to obtain 800 mesh (whiteness 72.9%) powder, and charcoal is added (the amount is 2.5% of the weight of the powder) ) and sodium chloride (the amount is 2.5% of the weight of the powder) and stir evenly, then put the material into a sagger, put it into a kiln (shuttle kiln), and calcinate at 1300°C for 6 hours, cool the material, and Disintegration in the disintegrator (the processing output of the disintegrator is 1.6 tons / hour), modification. Heat the FT-4 aluminum-titanium composite coupling agent to 100°C for melting, adjust the flow rate of the automatic dosing pump, the flow rate of the FT-4 aluminum-titanium composite coupling agent is 12 kg / hour, and the flow rate of the silane coupling agent KH570 At 12 kg / hour, the two active agents are simultaneously sprayed into the dispersion machine barrel for activation treatment to prod...
PUM
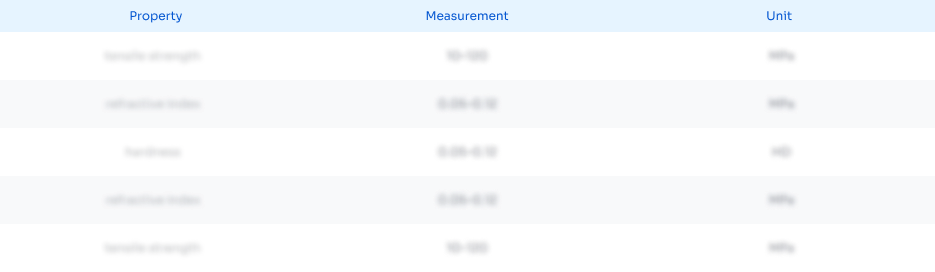
Abstract
Description
Claims
Application Information

- R&D Engineer
- R&D Manager
- IP Professional
- Industry Leading Data Capabilities
- Powerful AI technology
- Patent DNA Extraction
Browse by: Latest US Patents, China's latest patents, Technical Efficacy Thesaurus, Application Domain, Technology Topic, Popular Technical Reports.
© 2024 PatSnap. All rights reserved.Legal|Privacy policy|Modern Slavery Act Transparency Statement|Sitemap|About US| Contact US: help@patsnap.com