Mechanical arm modular joint with redundant degree of freedom
A technology of modular joints and degrees of freedom, used in manipulators, manufacturing tools, joints, etc., can solve the problems of low joint integration, low load-to-weight ratio, and large volume, and achieve small size, low weight, and high load-to-weight ratio. Effect
- Summary
- Abstract
- Description
- Claims
- Application Information
AI Technical Summary
Problems solved by technology
Method used
Image
Examples
Embodiment 1
[0029] refer to Figure 1-Figure 5 , this embodiment provides a modular joint of a redundant degree of freedom manipulator, especially a lightweight redundant degree of freedom manipulator modular joint with a hollow structure, which includes a joint fixing part, a power assembly and an electrical part composition;
[0030] The joint fixing part includes a joint fixing end cover 1 , a driver bracket 3 , a brake fixing housing 4 , a motor fixing housing 12 and a harmonic reducer fixing housing 15 .
[0031] The joint fixing end cover 1 is fixed on the left end of the brake fixing housing 4 to close the left end of the brake fixing housing 4, and in this embodiment, the left end of the brake fixing housing 4 is the redundant degree of freedom The power input end of the modular joint of the mechanical arm; the right end of the fixed brake housing 4 is fixed to the left end of the fixed motor housing 12 , and the fixed housing 15 of the harmonic reducer is fixed to the right end ...
PUM
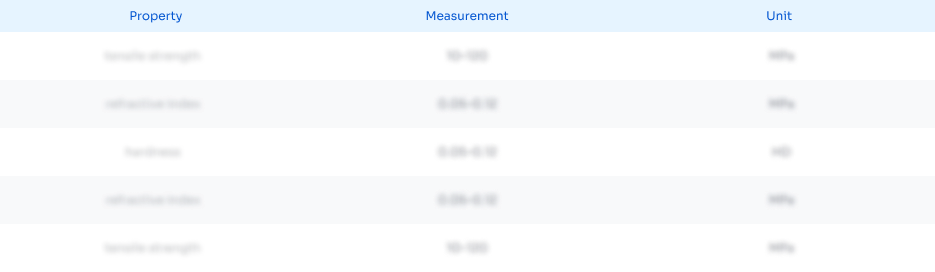
Abstract
Description
Claims
Application Information

- R&D Engineer
- R&D Manager
- IP Professional
- Industry Leading Data Capabilities
- Powerful AI technology
- Patent DNA Extraction
Browse by: Latest US Patents, China's latest patents, Technical Efficacy Thesaurus, Application Domain, Technology Topic, Popular Technical Reports.
© 2024 PatSnap. All rights reserved.Legal|Privacy policy|Modern Slavery Act Transparency Statement|Sitemap|About US| Contact US: help@patsnap.com