Method and exhaust gas aftertreatment system for determining load of particle-filtering assembly
A technology of exhaust gas post-processing and equipment, which is applied in the direction of exhaust gas treatment, electronic control of exhaust gas treatment devices, diagnostic devices of exhaust gas treatment devices, etc., and can solve problems such as difficulties
- Summary
- Abstract
- Description
- Claims
- Application Information
AI Technical Summary
Problems solved by technology
Method used
Image
Examples
Embodiment Construction
[0026] figure 1 Illustratively shows a simplified schematic diagram of an air and exhaust gas guide in a motor vehicle environment with an internal combustion engine 10 in which the method according to the invention can be applied. Before the supply air flow 21 is delivered via the compression stage 24 of the turbocharger 23 and the throttle valve 25 of the internal combustion engine 10, the supply air flow 21 first passes through the air quality sensor 22 through the air delivery passage 20. In the internal combustion engine 10, the air is converted in an exothermic manner together with the delivered fuel (not shown here). The generated exhaust gas can partly be re-transmitted to the supply air flow 21 via the exhaust gas recirculation 26. The remaining exhaust gas flow 32 is firstly guided via the exhaust gas turbine 31 of the turbocharger 23 via the exhaust duct 30 and then enters the exhaust gas aftertreatment device 40. A four-way catalyst 41 is arranged in the exhaust g...
PUM
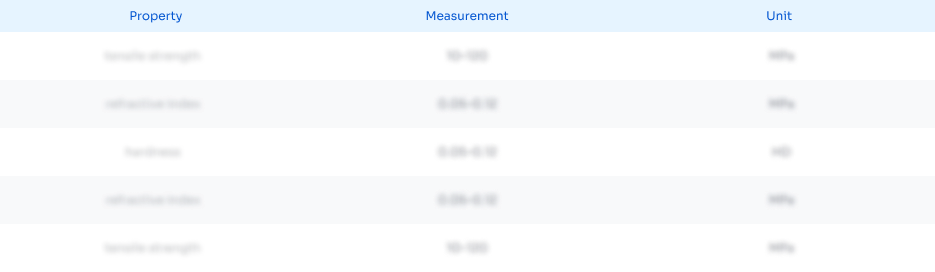
Abstract
Description
Claims
Application Information

- R&D
- Intellectual Property
- Life Sciences
- Materials
- Tech Scout
- Unparalleled Data Quality
- Higher Quality Content
- 60% Fewer Hallucinations
Browse by: Latest US Patents, China's latest patents, Technical Efficacy Thesaurus, Application Domain, Technology Topic, Popular Technical Reports.
© 2025 PatSnap. All rights reserved.Legal|Privacy policy|Modern Slavery Act Transparency Statement|Sitemap|About US| Contact US: help@patsnap.com