A method and device for measuring the telescopic displacement of an underground telescopic hollow mechanism
A hollow and displacement technology, applied in the field of civil engineering, can solve the problems of inconvenient measurement of the telescopic displacement of the telescopic mechanism, complex underground environment, and inconvenience of knowing the working state of the telescopic mechanism, etc. light weight effect
- Summary
- Abstract
- Description
- Claims
- Application Information
AI Technical Summary
Problems solved by technology
Method used
Image
Examples
Embodiment Construction
[0026] A device for measuring telescopic displacement of an underground retractable hollow mechanism, comprising a PC terminal 1, an above-ground module 2, and an underground module 3. The PC terminal 1 is connected to the above-ground module 2 , and the above-ground module 2 is in communication with the underground module 3 , and the underground module 3 is installed in the retractable hollow mechanism 4 .
[0027] The PC terminal 1 and the ground module 2 are on the ground, and jointly realize the control and modulation of the transmitted signal; the conditioning, frequency mixing and filtering, collection and processing, and distance measurement and display of the received signal.
[0028] The underground module 3 expands and contracts synchronously with the retractable hollow mechanism 4, and realizes signal laser emission, reception and photoelectric conversion during displacement measurement.
[0029] The PC terminal 1 is connected to the above-ground module 2 through a ...
PUM
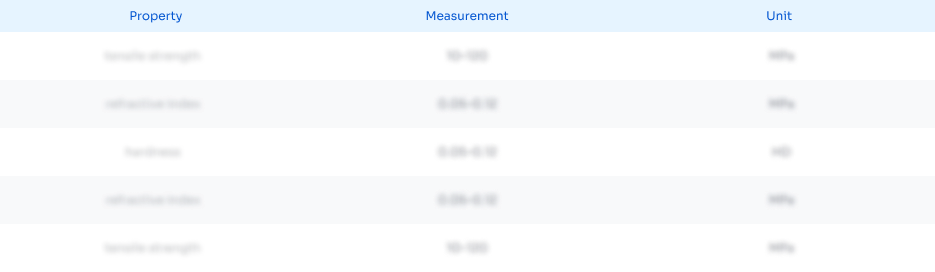
Abstract
Description
Claims
Application Information

- Generate Ideas
- Intellectual Property
- Life Sciences
- Materials
- Tech Scout
- Unparalleled Data Quality
- Higher Quality Content
- 60% Fewer Hallucinations
Browse by: Latest US Patents, China's latest patents, Technical Efficacy Thesaurus, Application Domain, Technology Topic, Popular Technical Reports.
© 2025 PatSnap. All rights reserved.Legal|Privacy policy|Modern Slavery Act Transparency Statement|Sitemap|About US| Contact US: help@patsnap.com