Production method of high-speed railway track board not requiring steam curing and special concrete
A technology for steam curing and track slabs, which is applied to early-strength and high-durability prestressed track slab concrete products, production methods and special concrete for high-speed rail track slabs, preparation of steam-free curing, high-strength fields, and can solve complex processes and curing time. Long, compact and other problems, to achieve the effect of simple preparation method, improved quality and production efficiency, and low production cost
- Summary
- Abstract
- Description
- Claims
- Application Information
AI Technical Summary
Problems solved by technology
Method used
Examples
Embodiment 1
[0015] The special steam-free concrete for the production of high-speed rail track slabs is characterized in that it is made by mixing and stirring the following components according to the weight ratio: PO42.5R grade ordinary Portland cement: 360 parts; slag powder: 80 parts; High Belite sulfoaluminate cement: 40 parts; activator: 1 part; early strength agent: 1 part; water reducing agent: 1.5 parts; anti-cracking and impermeable composite material: 1 part; 1169.5 parts; water: 87.5 parts.
[0016] The activator is a mixture of calcium oxide, calcium nitrite and calcium sulfate, and the weight ratio of calcium oxide, calcium nitrite and calcium sulfate is 50:20:30.
[0017] The accelerator is a mixture of triisopropanolamine, lithium carbonate and calcium formate, and the weight ratio of triisopropanolamine, lithium carbonate and calcium formate is 50:20:30.
[0018] The described water reducer is a powdery polycarboxylate water reducer.
[0019] The high belite sulfoalumin...
Embodiment 2
[0025] The steam-free maintenance-free concrete for the production of high-speed rail track slabs is characterized in that it is made by mixing and stirring the following components according to the weight ratio: PO42.5R grade ordinary Portland cement: 380 parts; slag powder: 60 parts; High Belite sulfoaluminate cement: 40 parts; activator: 1 part; early strength agent: 1.5 parts; water reducing agent: 1.5 parts; anti-crack and impermeability composite material: 1 part; 1169 parts; water: 87.5 parts.
[0026] The activator is a mixture of calcium oxide, calcium nitrite and calcium sulfate, and the weight ratio of calcium oxide, calcium nitrite and calcium sulfate is 50:30:20.
[0027] The accelerator is a mixture of triisopropanolamine, lithium carbonate and calcium formate, and the weight ratio of triisopropanolamine, lithium carbonate and calcium formate is 50:30:20.
[0028] The water reducer is a powdery amino acid water reducer.
[0029] The high belite sulfoaluminate c...
Embodiment 3
[0035] The special steam-free concrete for the production of high-speed rail track slabs is characterized in that it is made by mixing and stirring the following components according to the weight ratio: PO42.5R grade ordinary Portland cement: 360 parts; slag powder: 80 parts; High Belite sulfoaluminate cement: 40 parts; activator: 1 part; early strength agent: 1.5 parts; water reducing agent: 1.5 parts; anti-crack and impermeability composite material: 1 part; 1169 parts; water: 87.5 parts.
[0036] The activator is a mixture of calcium oxide, calcium nitrite and calcium sulfate, and the weight ratio of calcium oxide, calcium nitrite and calcium sulfate is 50:10:40.
[0037] The accelerator is a mixture of triisopropanolamine, lithium carbonate and calcium formate, and the weight ratio of triisopropanolamine, lithium carbonate and calcium formate is 50:10:40.
[0038] The water reducer is a powdery high-efficiency naphthalene-based water reducer.
[0039] The high belite su...
PUM
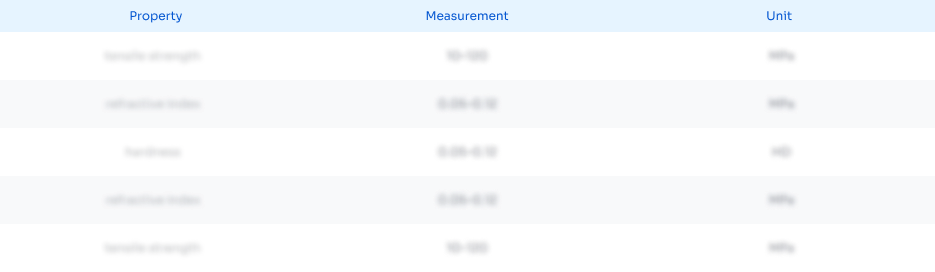
Abstract
Description
Claims
Application Information

- Generate Ideas
- Intellectual Property
- Life Sciences
- Materials
- Tech Scout
- Unparalleled Data Quality
- Higher Quality Content
- 60% Fewer Hallucinations
Browse by: Latest US Patents, China's latest patents, Technical Efficacy Thesaurus, Application Domain, Technology Topic, Popular Technical Reports.
© 2025 PatSnap. All rights reserved.Legal|Privacy policy|Modern Slavery Act Transparency Statement|Sitemap|About US| Contact US: help@patsnap.com