Hydraulic driving flexible robot joint
A robot joint and flexible technology, applied in the field of bionic robots, can solve problems such as heavy weight, disadvantageous robots, increase the complexity and nonlinearity of motor dynamics modeling, and achieve improved motion efficiency, reduced energy consumption, and reduced overall weight. Effect
- Summary
- Abstract
- Description
- Claims
- Application Information
AI Technical Summary
Benefits of technology
Problems solved by technology
Method used
Image
Examples
Embodiment Construction
[0020] In order to make the object, technical solution and advantages of the present invention clearer, the present invention will be further described in detail below in conjunction with the accompanying drawings and embodiments. It should be understood that the specific embodiments described here are only used to explain the present invention, not to limit the present invention. In addition, the technical features involved in the various embodiments of the present invention described below can be combined with each other as long as they do not constitute a conflict with each other.
[0021] refer to Figure 1 ~ Figure 3 , a hydraulically driven flexible robot joint, including a thigh structure 1, a thigh structure 2 and a lower leg structure 3, wherein,
[0022] The thigh structure 1 includes a thigh main frame 11, a cylinder base 12, a hydraulic cylinder 13, a moving frame 14, a guide shaft 15 and a compression spring 16, and the cylinder base 12 is hinged to the thigh mai...
PUM
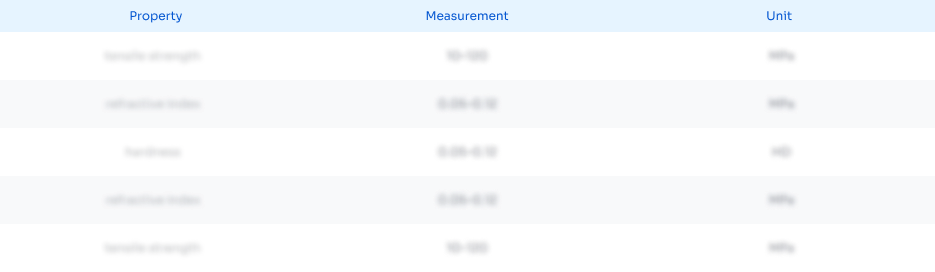
Abstract
Description
Claims
Application Information

- Generate Ideas
- Intellectual Property
- Life Sciences
- Materials
- Tech Scout
- Unparalleled Data Quality
- Higher Quality Content
- 60% Fewer Hallucinations
Browse by: Latest US Patents, China's latest patents, Technical Efficacy Thesaurus, Application Domain, Technology Topic, Popular Technical Reports.
© 2025 PatSnap. All rights reserved.Legal|Privacy policy|Modern Slavery Act Transparency Statement|Sitemap|About US| Contact US: help@patsnap.com