Zero calibration method for humanoid robot joints
A humanoid robot and robot technology, applied in the field of humanoid robots, can solve the problems of high cost, complex equipment development technology, narrow application scope, etc., and achieve the effect of saving device cost, reducing human operation error, and saving development cost.
- Summary
- Abstract
- Description
- Claims
- Application Information
AI Technical Summary
Problems solved by technology
Method used
Image
Examples
Embodiment Construction
[0026] A method for calibrating the zero position of a humanoid robot joint according to the present invention is performed in sequence according to the following steps:
[0027] Step 1: Use PC software and mobile APP to connect to the humanoid robot through wired or wireless connection, or send out joint zero calibration commands to the humanoid robot through voice control, and the humanoid robot control center will enter zero. Bit calibration mode, start calibrating each joint;
[0028] Step 2: During zero-position calibration, the humanoid robot control center sends a rotation command to the joint to be calibrated; the robot control center queries the angle of the joint to be calibrated at intervals, and when the joint to be calibrated cannot rotate, it is considered that the joint to be calibrated has rotated To the joint limit surface, the robot control center calculates the zero position error value, saves it, and starts to calibrate the next joint zero position. like ...
PUM
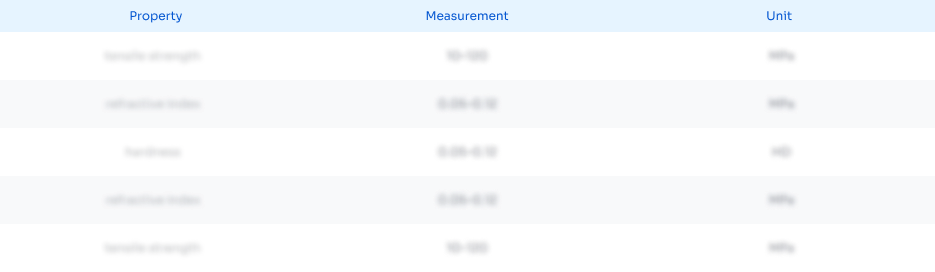
Abstract
Description
Claims
Application Information

- R&D Engineer
- R&D Manager
- IP Professional
- Industry Leading Data Capabilities
- Powerful AI technology
- Patent DNA Extraction
Browse by: Latest US Patents, China's latest patents, Technical Efficacy Thesaurus, Application Domain, Technology Topic, Popular Technical Reports.
© 2024 PatSnap. All rights reserved.Legal|Privacy policy|Modern Slavery Act Transparency Statement|Sitemap|About US| Contact US: help@patsnap.com