Apparatus for measuring plane stress of anisotropic material
A technology of plane stress and anisotropy, applied in the direction of measuring devices, measuring forces, instruments, etc., can solve the problems of low measurement accuracy and achieve the effects of high measurement efficiency, high precision, and easy operation
- Summary
- Abstract
- Description
- Claims
- Application Information
AI Technical Summary
Problems solved by technology
Method used
Image
Examples
specific Embodiment approach 1
[0036] Specific implementation mode one: combine figure 1 Describe this embodiment, the device for measuring the plane stress of anisotropic materials in this embodiment includes an ultrasonic transducer group, an ultrasonic oblique incidence wedge 2, a signal generator 3, a digital oscilloscope 4 and an analysis and processing software 5;
[0037] The shape of the ultrasonic oblique incidence wedge 2 is a regular octagon, and the oblique incidence angle is 34°.
[0038] The ultrasonic transducer group includes a first ultrasonic longitudinal wave excitation probe 11, a second ultrasonic longitudinal wave excitation probe 12, a third ultrasonic longitudinal wave excitation probe 13, a first ultrasonic longitudinal wave receiving probe 14, a second ultrasonic longitudinal wave receiving probe 15 and a third ultrasonic longitudinal wave receiving probe 15. Ultrasonic longitudinal wave receiving probe 16, six probes are fixedly connected with ultrasonic oblique incidence wedge 2,...
specific Embodiment approach 2
[0043] Embodiment 2: This embodiment differs from Embodiment 1 in that: the ultrasonic oblique incidence wedge 2 is made of polytetrafluoroethylene. Others are the same as in the first embodiment.
specific Embodiment approach 3
[0044] Embodiment 3: This embodiment differs from Embodiment 1 or Embodiment 2 in that: the center of the ultrasonic oblique incidence wedge 2 is embedded with a NdFeB magnet 7 . Others are the same as in the first or second embodiment.
PUM
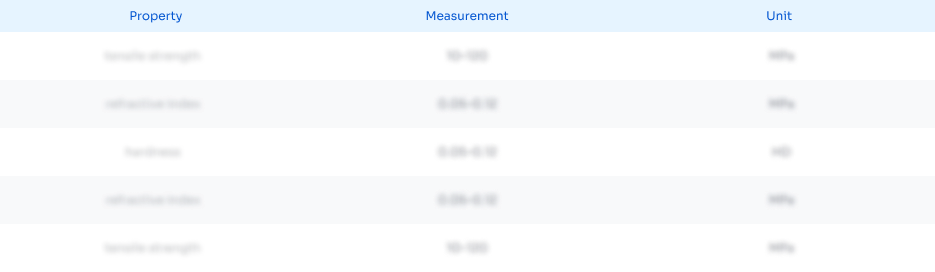
Abstract
Description
Claims
Application Information

- Generate Ideas
- Intellectual Property
- Life Sciences
- Materials
- Tech Scout
- Unparalleled Data Quality
- Higher Quality Content
- 60% Fewer Hallucinations
Browse by: Latest US Patents, China's latest patents, Technical Efficacy Thesaurus, Application Domain, Technology Topic, Popular Technical Reports.
© 2025 PatSnap. All rights reserved.Legal|Privacy policy|Modern Slavery Act Transparency Statement|Sitemap|About US| Contact US: help@patsnap.com