Strain sensor for weft knitted fabric and knitting method
A technology of strain sensors and knitted fabrics, which is applied in weft knitting, knitting, textiles and papermaking, etc. It can solve problems such as easy detachment and curling of coil courses, small sensor sensitivity coefficient, and sensor application limitations, so as to avoid detachment And curling, overall uniform structure, good extensibility and elastic recovery
- Summary
- Abstract
- Description
- Claims
- Application Information
AI Technical Summary
Problems solved by technology
Method used
Image
Examples
Embodiment
[0044] Such as figure 1 As shown, a weft-knitted fabric strain sensor includes an induction area 1 and a connection area 2, and the induction area 1 is composed of a plain stitch plated coil in which the veil is a conductive yarn and the ground yarn is an elastic yarn. The connection area 2 is located on both sides of the induction area 1, and the connection area 2 is composed of a plain needle plated coil in which the veil is a yarn and the ground yarn is an elastic yarn, and also includes an overlock area 3, and the overlock area 3 Located on the outside of each corresponding connection area 2, the overlock area 3 is composed of flat-stitch plated loops in which the veil is a yarn and the ground yarn is an elastic yarn, wherein the veil is exposed in the induction area 1, the connection area 2 and the lock On the front side of the edge area 3, the ground yarn is exposed on the reverse side of the sensing area 1, the connecting area 2 and the overlock area 3, and the conducti...
PUM
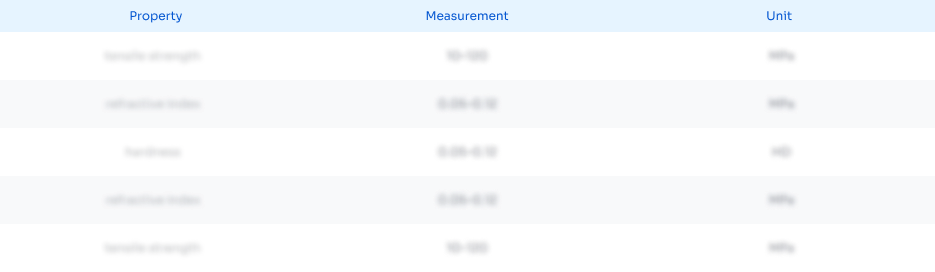
Abstract
Description
Claims
Application Information

- R&D
- Intellectual Property
- Life Sciences
- Materials
- Tech Scout
- Unparalleled Data Quality
- Higher Quality Content
- 60% Fewer Hallucinations
Browse by: Latest US Patents, China's latest patents, Technical Efficacy Thesaurus, Application Domain, Technology Topic, Popular Technical Reports.
© 2025 PatSnap. All rights reserved.Legal|Privacy policy|Modern Slavery Act Transparency Statement|Sitemap|About US| Contact US: help@patsnap.com