Flexible claw of translational motion type robot
A robot, translational technology, applied in the field of robots, can solve the problems of lack of flexibility, transmission error, complex structure, etc., and achieve the effects of convenient maintenance, novel design and simple operation.
- Summary
- Abstract
- Description
- Claims
- Application Information
AI Technical Summary
Problems solved by technology
Method used
Image
Examples
Embodiment
[0020] A flexible gripper of a translational robot, including a gripper part, a housing part and a flexible driving part;
[0021] The claw part uses a flexible hinge as a kinematic joint and is provided with a parallelogram structure to form two fingers with no external friction, no transmission gap and an integrated structure, and the two fingers are symmetrically distributed; the fingers include fixed Knuckle 1, first flexible hinge 2, first transmission knuckle 3, second flexible hinge 4, second transmission knuckle 5, third flexible hinge 6, fourth flexible hinge 7, clamping knuckle 8, fifth Flexible hinge 9, third transmission knuckle 10, sixth flexible hinge 11, fourth transmission knuckle 12, seventh flexible hinge 13, driving surface 14; one end of the first transmission knuckle 3 passes through the first flexible hinge 2 and the fixed finger joint 1, and the other end connects to the clamping knuckle 8 through the third flexible hinge 6, and the first flexible hinge ...
PUM
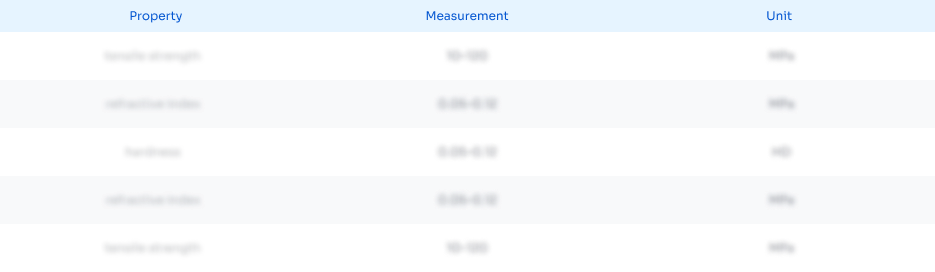
Abstract
Description
Claims
Application Information

- R&D Engineer
- R&D Manager
- IP Professional
- Industry Leading Data Capabilities
- Powerful AI technology
- Patent DNA Extraction
Browse by: Latest US Patents, China's latest patents, Technical Efficacy Thesaurus, Application Domain, Technology Topic, Popular Technical Reports.
© 2024 PatSnap. All rights reserved.Legal|Privacy policy|Modern Slavery Act Transparency Statement|Sitemap|About US| Contact US: help@patsnap.com