High-frequency start-stop traction system
A traction system and high-frequency technology, which is applied in the field of material loss prevention traction system, can solve the problems of scratched material belt, brittle material belt breakage, and the clamping force should not be too large, so as to achieve the effect of maintaining accuracy.
- Summary
- Abstract
- Description
- Claims
- Application Information
AI Technical Summary
Problems solved by technology
Method used
Image
Examples
Embodiment Construction
[0011] The specific implementation manners of the present invention will be described in detail below in conjunction with the accompanying drawings.
[0012] Such as figure 1 and figure 2 As shown, the high-frequency start-stop traction system of the present invention mainly includes a magnetic track and a support mechanism 35 matched with the magnetic track 36. An iron core coil 310 is arranged in the magnetic track 35, and a material belt clamping mechanism 35 is provided on the support mechanism 35. Mechanism, change the clamping mechanism to fix a number of upper jaws 33 and lower jaws 34 that cooperate with each other, wherein a number of vacuum suction heads 32 are arranged on the upper jaws or lower jaws, and the upper jaws or lower jaws can move up and down Clamp the strip tightly.
[0013] In this embodiment, the vacuum suction head 32 is arranged on the upper jaw 33, and the bracket mechanism is provided with a fixed plate 312 for installing the jaws. The fixed pl...
PUM
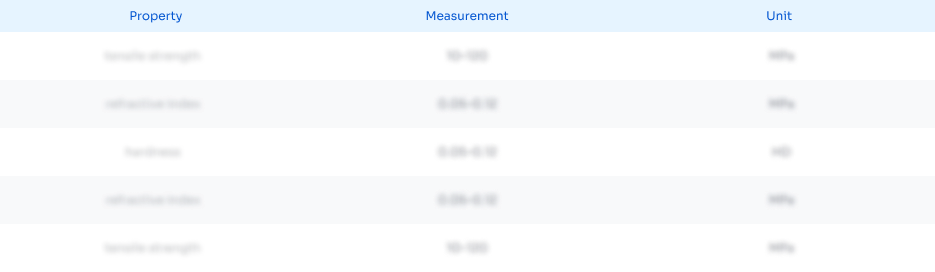
Abstract
Description
Claims
Application Information

- R&D
- Intellectual Property
- Life Sciences
- Materials
- Tech Scout
- Unparalleled Data Quality
- Higher Quality Content
- 60% Fewer Hallucinations
Browse by: Latest US Patents, China's latest patents, Technical Efficacy Thesaurus, Application Domain, Technology Topic, Popular Technical Reports.
© 2025 PatSnap. All rights reserved.Legal|Privacy policy|Modern Slavery Act Transparency Statement|Sitemap|About US| Contact US: help@patsnap.com