A method for increasing the content of tricalcium silicate in Portland cement powder
A technology for Portland cement and tricalcium silicate is applied in the field of increasing the content of tricalcium silicate mineral crystals in cement powder, which can solve the problems of unobtained and other problems, and achieve the effects of low energy consumption and simple separation and enrichment process.
- Summary
- Abstract
- Description
- Claims
- Application Information
AI Technical Summary
Problems solved by technology
Method used
Image
Examples
Embodiment 1
[0016] Add 20 grams of 15% Portland cement with 45 micron sieves to a centrifuge tube, add 100 ml of 1# heavy liquid, and centrifuge at 8000 rpm for 5 minutes, then pour out the heavy liquid and the upper layer of cement powder, such as For 2# heavy liquid, centrifuge at 8000rpm for 5 minutes, pour out the heavy liquid and the upper layer of cement powder, and filter to obtain the upper layer of cement powder. The XRD test results are shown in the attached figure 1 , from which it can be seen that tricalcium silicate is significantly improved, and the semi-quantitative analysis of tricalcium silicate content exceeds wt80%.
Embodiment 2
[0018] 20 grams of Portland cement with 15% of 45 micron sieve, add 120 ml of 1# heavy liquid to the centrifuge tube, centrifuge at 10000rpm for 8 minutes, pour out the heavy liquid and the upper layer of cement powder, such as For 2# heavy liquid, centrifuge at 10000rpm for 8 minutes, pour out the heavy liquid and the upper layer of cement powder, and filter to obtain the upper layer of cement powder. The XRD test results are shown in the attached figure 1 , from which it can be seen that tricalcium silicate is significantly improved, and the semi-quantitative analysis of tricalcium silicate content exceeds wt83%.
Embodiment 3
[0020] Add 20 grams of 19% Portland cement with a 45-micron sieve to the centrifuge tube, add 110 ml of 1# heavy liquid, and centrifuge at 9000 rpm for 9 minutes, then pour out the heavy liquid and the upper layer of cement powder, such as For 2# heavy liquid, centrifuge at 9000rpm for 9 minutes, pour out the heavy liquid and the upper layer of cement powder, and filter to obtain the upper layer of cement powder. The XRD test results are shown in the attached figure 1 , from which it can be seen that tricalcium silicate is significantly improved, and the semi-quantitative analysis of tricalcium silicate content exceeds wt82%.
PUM
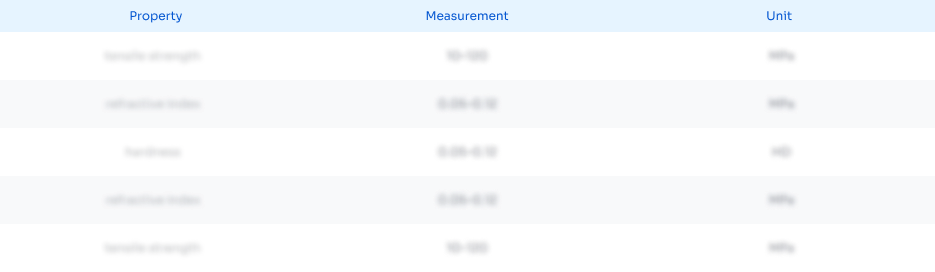
Abstract
Description
Claims
Application Information

- R&D
- Intellectual Property
- Life Sciences
- Materials
- Tech Scout
- Unparalleled Data Quality
- Higher Quality Content
- 60% Fewer Hallucinations
Browse by: Latest US Patents, China's latest patents, Technical Efficacy Thesaurus, Application Domain, Technology Topic, Popular Technical Reports.
© 2025 PatSnap. All rights reserved.Legal|Privacy policy|Modern Slavery Act Transparency Statement|Sitemap|About US| Contact US: help@patsnap.com