Preparation method of sodium silicate
A technology of sodium silicate and sodium carbonate, applied in the direction of silicate, alkali metal silicate, etc., can solve the problem that fluorine-containing silicon slag cannot be recycled
- Summary
- Abstract
- Description
- Claims
- Application Information
AI Technical Summary
Problems solved by technology
Method used
Examples
Embodiment 1
[0014] Weigh 289.6g of fluorine-containing silicon slag, wash and filter each time with 100g of deionized water, wash and filter 4 times, wash the pH value of fluorine-containing silicon slag to 4.8, and dry the silicon slag for 8.5 hours to obtain 126.5 g dry silicon slag with a moisture content of 1.81%. Fully mix 126.5g of silicon slag and 106g of sodium carbonate obtained by drying treatment, put them into a high-temperature furnace after mixing evenly, turn on the negative pressure system, make the reaction system form a slight negative pressure of -0.01MPa, and water the The fluorine-containing gas is absorbed; after the temperature of the high-temperature furnace rises to 850°C, close the negative pressure system; the high-temperature furnace is heated to 1100°C-1150°C, and stays for 30 minutes. The actual reaction temperature of sodium carbonate and fluorine-containing silicon slag in the high-temperature furnace is 1070°C , reacted for 30 minutes; after the reaction w...
Embodiment 2
[0016] Weigh 320.5g of fluorine-containing silicon slag, wash and filter each time with 100g of deionized water, wash and filter 5 times, wash the pH value of fluorine-containing silicon slag to 5.2, and dry the silicon slag for 9 hours to obtain 141g Dry silicon slag with a moisture content of 1.78%. Fully mix 141g of silicon slag and 106g of sodium carbonate obtained by drying treatment, put them into a high-temperature furnace after mixing evenly, turn on the negative pressure system, make the reaction system form a slight negative pressure of -0.01MPa, and use water to remove the slag released from the high-temperature furnace. Fluorine gas is absorbed; after the temperature of the high-temperature furnace rises to 870°C, close the negative pressure system; heat the high-temperature furnace to 1150°C-1180°C, and stay for 30 minutes. The actual reaction temperature of sodium carbonate and fluorine-containing silicon slag in the high-temperature furnace is 1105°C. React for ...
Embodiment 3
[0018] Weigh 362.8g of fluorine-containing silicon slag, wash and filter each time with 100g of deionized water, wash and filter 6 times, wash the pH value of fluorine-containing silicon slag to 5.4, and dry the silicon slag for 10 hours to obtain 156g Dry silicon slag with a moisture content of 1.75%. Fully mix 156g of silicon slag and 106g of sodium carbonate obtained by drying treatment, put them into a high-temperature furnace after mixing evenly, turn on the negative pressure system, make the reaction system form a slight negative pressure of -0.01MPa, and use water to remove the slag released from the high-temperature furnace. Fluorine gas is absorbed; after the temperature of the high-temperature furnace rises to 880°C, close the negative pressure system; heat the high-temperature furnace to 1180°C-1200°C, and stay for 30 minutes. The actual reaction temperature of sodium carbonate and fluorine-containing silicon slag in the high-temperature furnace is 1136°C. React for...
PUM
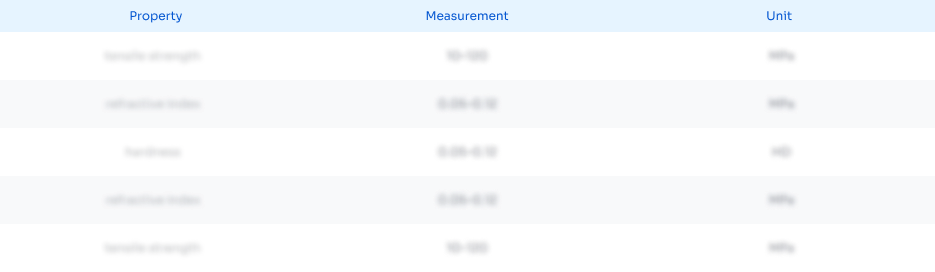
Abstract
Description
Claims
Application Information

- R&D Engineer
- R&D Manager
- IP Professional
- Industry Leading Data Capabilities
- Powerful AI technology
- Patent DNA Extraction
Browse by: Latest US Patents, China's latest patents, Technical Efficacy Thesaurus, Application Domain, Technology Topic, Popular Technical Reports.
© 2024 PatSnap. All rights reserved.Legal|Privacy policy|Modern Slavery Act Transparency Statement|Sitemap|About US| Contact US: help@patsnap.com