Process for producing regenerated rubber
A technology of recycled rubber and production technology, which is applied in the direction of mechanical material recycling, plastic recycling, recycling technology, etc. It can solve the problems of product quality cannot be improved, environmental pollution, foul smell, etc., and achieve safe material retrieving and operation, and no environmental pollution , Improve the effect of rubber quality
- Summary
- Abstract
- Description
- Claims
- Application Information
AI Technical Summary
Problems solved by technology
Method used
Examples
Embodiment 1
[0017] A production process of regenerated rubber of the present invention comprises the following steps: firstly, the waste rubber is selected, crushed by a crusher, and the fineness of the crushed rubber reaches 40 mesh, and then the crushed rubber is placed in a vulcanization pool for Desulfurization, adding additives, the additives are vegetable oil asphalt, softener and activator, heating continuously while stirring, the temperature is 300 ℃, the rubber after desulfurization is cooled in the cooling tower, and the cooled rubber in the pressing equipment The refining machine and the open mill are used to compress the tablets to make recycled rubber products.
Embodiment 2
[0019] A production process of reclaimed rubber according to the present invention comprises the following steps: firstly select the waste rubber, crush it with a crusher, the fineness of the crushed rubber reaches 35 mesh, and then place the crushed rubber in a vulcanization pool for Desulfurization, adding additives, the additives are vegetable oil asphalt, softener and activator, heating continuously while stirring, the temperature is 350 ℃, the rubber after desulfurization is cooled in the cooling tower, and the cooled rubber in the pressing equipment The refining machine and the open mill are used to compress the tablets to make recycled rubber products.
Embodiment 3
[0021] A production process of reclaimed rubber according to the present invention comprises the following steps: first, select the waste rubber, crush it with a crusher, the fineness of the crushed rubber reaches 30 mesh, and then place the crushed rubber in a vulcanization pool for Desulfurization, adding additives, the additives are vegetable oil asphalt, softener and activator, heating continuously while stirring, the temperature is 400 ℃, the rubber after desulfurization is cooled in the cooling tower, and the cooled rubber in the pressing equipment The refining machine and the open mill are used to compress the tablets to make recycled rubber products.
PUM
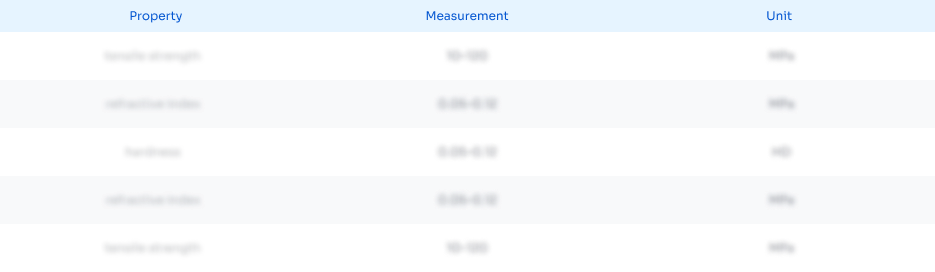
Abstract
Description
Claims
Application Information

- R&D
- Intellectual Property
- Life Sciences
- Materials
- Tech Scout
- Unparalleled Data Quality
- Higher Quality Content
- 60% Fewer Hallucinations
Browse by: Latest US Patents, China's latest patents, Technical Efficacy Thesaurus, Application Domain, Technology Topic, Popular Technical Reports.
© 2025 PatSnap. All rights reserved.Legal|Privacy policy|Modern Slavery Act Transparency Statement|Sitemap|About US| Contact US: help@patsnap.com