Novel fodder stacking mechanical arm adopting servo motors to drive multi-freedom-degree connecting rod mechanism
A technology of servo motor and link mechanism, applied in the direction of manipulator, program-controlled manipulator, claw arm, etc., can solve the problems of high precision requirements, low transmission efficiency, complex structure, etc., to overcome high precision requirements, good dynamic performance, inertia low effect
- Summary
- Abstract
- Description
- Claims
- Application Information
AI Technical Summary
Problems solved by technology
Method used
Image
Examples
Embodiment Construction
[0006] A new type of feed stacking mechanical arm driven by a servo motor with a multi-degree-of-freedom linkage mechanism, including a base 9, a first active rod 1, a second active rod 2, a third active rod 3, a third connecting rod 4, and a fourth connecting rod Rod 7, the first connecting rod 5, the big arm 6, the wrist 20, the claw 8 and the servo drive device; the base 9 is installed on the movable rotary platform; one end of the first active rod 1 passes through the first rotating pair 11 It is connected with the base 9, the other end is connected with the third connecting rod 4 through the fourth rotating pair 14, and the other end of the third connecting rod 4 is connected with the first connecting rod 5 through the fifth rotating pair 15; one end of the second active rod 2 Connect with the base 9 through the second rotating pair 12, and the other end is connected with the first connecting rod 5 through the sixth rotating pair 16; One end of the third active lever 3 is ...
PUM
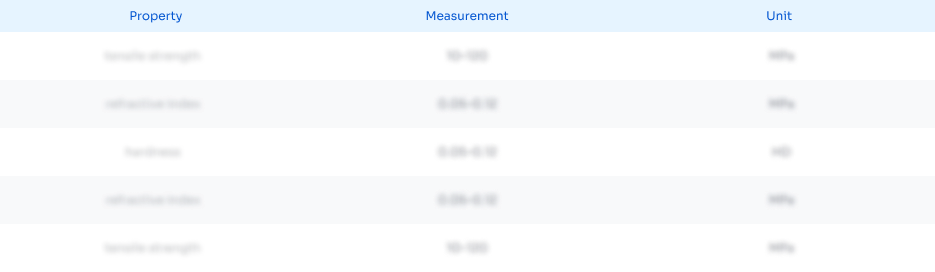
Abstract
Description
Claims
Application Information

- R&D
- Intellectual Property
- Life Sciences
- Materials
- Tech Scout
- Unparalleled Data Quality
- Higher Quality Content
- 60% Fewer Hallucinations
Browse by: Latest US Patents, China's latest patents, Technical Efficacy Thesaurus, Application Domain, Technology Topic, Popular Technical Reports.
© 2025 PatSnap. All rights reserved.Legal|Privacy policy|Modern Slavery Act Transparency Statement|Sitemap|About US| Contact US: help@patsnap.com