Method for producing a brush-commutated direct-current motor
A technology of DC motor and pole teeth, applied in the field of brushed commutation DC motor, can solve the problem of asymmetric commutation current, and achieve the effect of reducing the structure space
- Summary
- Abstract
- Description
- Claims
- Application Information
AI Technical Summary
Problems solved by technology
Method used
Image
Examples
Embodiment Construction
[0050] figure 1 A schematic illustration of a brush-commutated DC motor 1 with a stator 10 and a rotor 11 arranged on the stator 10 , rotatable about an axis of rotation D, is shown.
[0051] In a known manner, the stator 10 has a multiplicity of field poles M1 - M6 , which are formed by permanent magnets and arranged in the same manner on the stator 1 over a large area. Field poles M1 - M6 are directed towards rotor 11 by means of different, alternating poles N, S, so that in circumferential direction U south pole S always follows north pole S and vice versa.
[0052] In the exemplary embodiment shown, the stator 10 has exactly six field poles M1-M6.
[0053] The rotor 11 is arranged rotatably about the axis of rotation D on the stator 10 and, in the exemplary embodiment shown, has nine pole teeth Z1 - Z9 , which extend radially relative to the axis of rotation D along the direction of extension E, Pointing towards the stator 10 and separated from each other about the axis ...
PUM
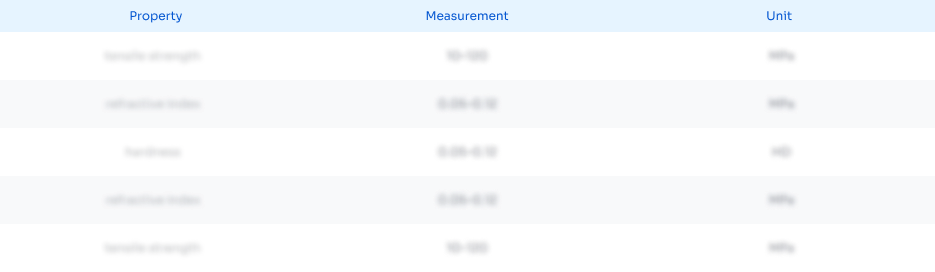
Abstract
Description
Claims
Application Information

- R&D Engineer
- R&D Manager
- IP Professional
- Industry Leading Data Capabilities
- Powerful AI technology
- Patent DNA Extraction
Browse by: Latest US Patents, China's latest patents, Technical Efficacy Thesaurus, Application Domain, Technology Topic, Popular Technical Reports.
© 2024 PatSnap. All rights reserved.Legal|Privacy policy|Modern Slavery Act Transparency Statement|Sitemap|About US| Contact US: help@patsnap.com