Vibration analysis and noise estimation method for coaxial dual-output planetary reducer
A planetary reducer, vibration analysis technology, used in instruments, special data processing applications, electrical digital data processing, etc.
- Summary
- Abstract
- Description
- Claims
- Application Information
AI Technical Summary
Problems solved by technology
Method used
Examples
Embodiment Construction
[0013] A vibration analysis and noise estimation method of a coaxial double output planetary reducer, comprising the following steps:
[0014] The first step: Apply the self-developed three-dimensional dynamic contact finite element analysis program of gears to calculate the time-varying stiffness excitation, error excitation and meshing impact excitation of gear meshing;
[0015] The second step: use I-DEAS software to establish the finite element model of the coaxial double output planetary gear reducer;
[0016] The third step: conduct simulation analysis on the inherent characteristics of the reducer and the dynamic response and structural noise under the internal dynamic excitation.
[0017] Calculations show that the natural frequency of the gearbox does not coincide with the rotational frequency of the transmission shaft or the meshing frequency of the gears, and the maximum value of the structural noise appears near the meshing frequency of the gears.
[0018] The abo...
PUM
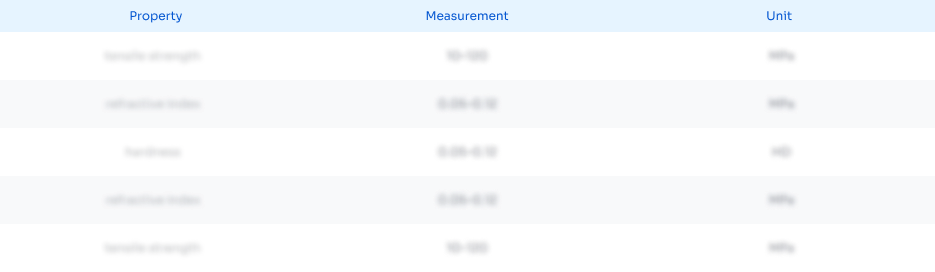
Abstract
Description
Claims
Application Information

- Generate Ideas
- Intellectual Property
- Life Sciences
- Materials
- Tech Scout
- Unparalleled Data Quality
- Higher Quality Content
- 60% Fewer Hallucinations
Browse by: Latest US Patents, China's latest patents, Technical Efficacy Thesaurus, Application Domain, Technology Topic, Popular Technical Reports.
© 2025 PatSnap. All rights reserved.Legal|Privacy policy|Modern Slavery Act Transparency Statement|Sitemap|About US| Contact US: help@patsnap.com