High-precision stress wave signal acquisition method and equipment
A technology of signal acquisition and stress wave, which is applied to the analysis of solids using sound waves/ultrasonic waves/infrasonic waves, material analysis using sound waves/ultrasonic waves/infrasonic waves, and measuring devices. It can solve the problems of low signal acquisition accuracy, low signal-to-noise ratio, and dynamic range. Small problems, to achieve the effect of reducing noise interference, improving effective accuracy, and high detection accuracy
- Summary
- Abstract
- Description
- Claims
- Application Information
AI Technical Summary
Problems solved by technology
Method used
Image
Examples
Embodiment
[0039] A high-precision stress wave signal acquisition method specifically includes the following steps:
[0040] (1) Use the excitation device to strike the anchor rod to generate a stress wave signal;
[0041] (2) Using a piezoelectric sensor to collect the stress wave signal generated by knocking;
[0042] (3) The stress wave signal enters the signal amplification circuit to amplify the signal;
[0043] (4) The amplified signal enters the low-pass filter circuit to filter out the interference signal;
[0044] (5) The output signal V of the low-pass filter circuit out4 On the one hand, it is sent to the voltage comparison circuit, and on the other hand, it is sent to the program-controlled amplifier circuit;
[0045] (6) The voltage comparison circuit compares the filtered signal with the reference voltage, and the high level or low level output after comparison is sent to the FPGA controller;
[0046] (7) The FPGA controller sends the encoded values A0 and A1 to the p...
PUM
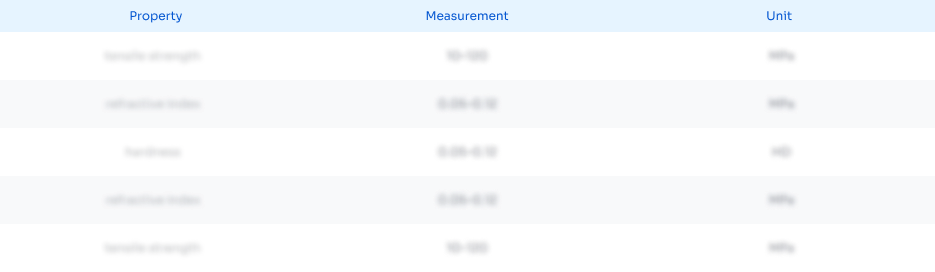
Abstract
Description
Claims
Application Information

- Generate Ideas
- Intellectual Property
- Life Sciences
- Materials
- Tech Scout
- Unparalleled Data Quality
- Higher Quality Content
- 60% Fewer Hallucinations
Browse by: Latest US Patents, China's latest patents, Technical Efficacy Thesaurus, Application Domain, Technology Topic, Popular Technical Reports.
© 2025 PatSnap. All rights reserved.Legal|Privacy policy|Modern Slavery Act Transparency Statement|Sitemap|About US| Contact US: help@patsnap.com