A method for realizing three-layer four-station injection molding of thick-walled parts
A realization method, four-station technology, applied in the direction of household components, household appliances, other household appliances, etc., can solve the problems of limited scope of application, long cycle, etc., to achieve the reduction of injection molding cycle, time reduction, and injection waiting time reduction Effect
- Summary
- Abstract
- Description
- Claims
- Application Information
AI Technical Summary
Problems solved by technology
Method used
Image
Examples
Embodiment Construction
[0031] First inject the middle layer (serial number 1), then inject the lower side (sequence number 3) of the outer periphery of the middle layer, and finally inject the upper side (serial number 2) of the outer periphery of the middle layer; a fixed mold and a movable mold are set to realize injection molding (see figure 2 );
[0032] The specific steps are:
[0033] (1) No. 1 fixed mold and No. 1 moving mold are injected into the middle layer;
[0034] (2) The middle layer stays on the No. 1 movable mold side, rotates 90 degrees, and closes the mold;
[0035] (3) No. 1 fixed mold and No. 2 dynamic mold inject the middle layer; the middle layer of the mold opening is left on the side of the No. 2 moving mold; the No. 3 fixed mold and the No. 1 moving mold are used as cooling chambers; the middle layer of the mold opening is left on the No. 3 side Fixed mold side; reverse rotation 90 degrees;
[0036] (4) No. 1 fixed mold and No. 1 dynamic mold inject the middle layer; the...
PUM
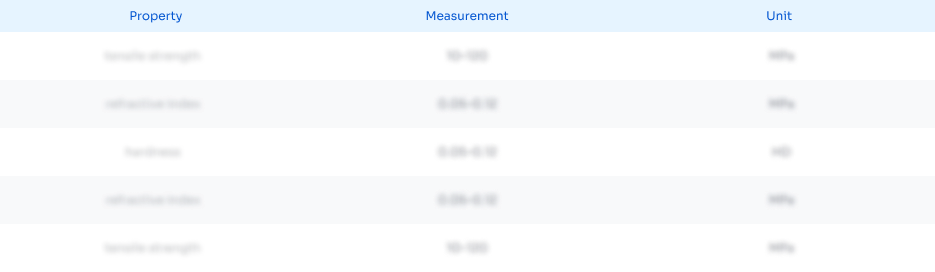
Abstract
Description
Claims
Application Information

- R&D Engineer
- R&D Manager
- IP Professional
- Industry Leading Data Capabilities
- Powerful AI technology
- Patent DNA Extraction
Browse by: Latest US Patents, China's latest patents, Technical Efficacy Thesaurus, Application Domain, Technology Topic, Popular Technical Reports.
© 2024 PatSnap. All rights reserved.Legal|Privacy policy|Modern Slavery Act Transparency Statement|Sitemap|About US| Contact US: help@patsnap.com