Aircraft panel butt joint structure
A technology of aircraft siding and siding, which is applied in aircraft assembly and other directions, can solve problems such as low assembly efficiency, hindering docking work, and docking misalignment, and achieves the effects of improving assembly efficiency, avoiding docking misalignment, and ensuring no deformation
- Summary
- Abstract
- Description
- Claims
- Application Information
AI Technical Summary
Problems solved by technology
Method used
Image
Examples
Embodiment Construction
[0016] The present invention will be further described below in conjunction with the accompanying drawings and specific embodiments.
[0017] Such as Figure 1 to Figure 4 As shown in , the aircraft panel docking structure of the present invention includes a first aircraft panel 1 and a second aircraft panel 2 to be butted, and the first aircraft panel 1 includes a first skin layer 11 and a first Skeleton layer 12; the second aircraft wall panel 2 includes a second skin layer 21 and a second skeleton layer 22, and a plurality of first butt joints 31 are arranged at intervals along the butt edge of the first aircraft wall panel 1, so The first butt joint 31 is detachably installed on the first aircraft wall panel 1, and the first butt joint 31 is connected with the first skin layer 11 and the first skeleton layer 12 at the same time; A plurality of second butt joints 32 are arranged at intervals on the butt joint edge, and the second butt joints 32 are detachably installed on ...
PUM
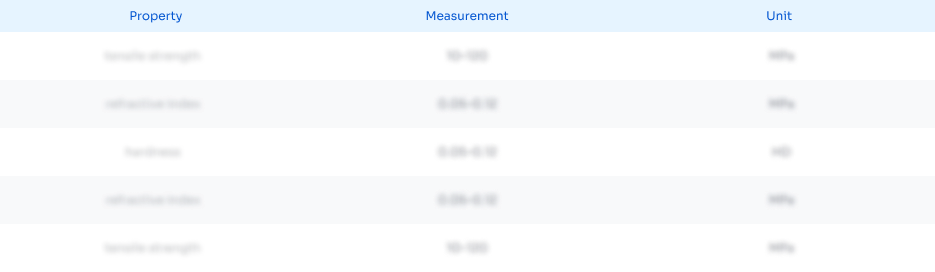
Abstract
Description
Claims
Application Information

- Generate Ideas
- Intellectual Property
- Life Sciences
- Materials
- Tech Scout
- Unparalleled Data Quality
- Higher Quality Content
- 60% Fewer Hallucinations
Browse by: Latest US Patents, China's latest patents, Technical Efficacy Thesaurus, Application Domain, Technology Topic, Popular Technical Reports.
© 2025 PatSnap. All rights reserved.Legal|Privacy policy|Modern Slavery Act Transparency Statement|Sitemap|About US| Contact US: help@patsnap.com