Rotor comprehensive testing table and corresponding testing method
A comprehensive test and rotor technology, applied in the field of comprehensive rotor test and rotor comprehensive test bench, can solve the problems of inability to detect the spatial distribution of magnetic steel magnetic field, inability to ensure the stability of motor finished products, inability to test the comprehensive performance of the rotor, etc. Ensure the effect of quality, comprehensive performance and stability
- Summary
- Abstract
- Description
- Claims
- Application Information
AI Technical Summary
Problems solved by technology
Method used
Image
Examples
Embodiment Construction
[0020] A rotor comprehensive test bench, see figure 1 : It includes a test control cabinet 1, a test tooling platform 2, a waveform imaging structure 3 is included on the test control cabinet 2, and a space magnetic field scanning device is arranged on the test control cabinet 2 (not shown in the figure, which belongs to the existing mature structure) , the test tooling table 1 includes a frame 4, and the upper end surface of the frame 4 is arranged with a rotor supporting frame 5 and a rotor driving shaft frame 6, and the rotor supporting frame 5 and the rotor driving rotating shaft frame 6 are respectively located on both sides of the upper end surface of the frame 4 Arrangement, the rotor support bracket 5 is used to support the mandrel 8 of the installed rotor 7, the rotor drive shaft frame 6 supports the rotor drive shaft 9, the rotor drive shaft 9 is connected to the output end of the rotating motor 10, and the mandrel 8 can be inserted into the rotor In the positioning ...
PUM
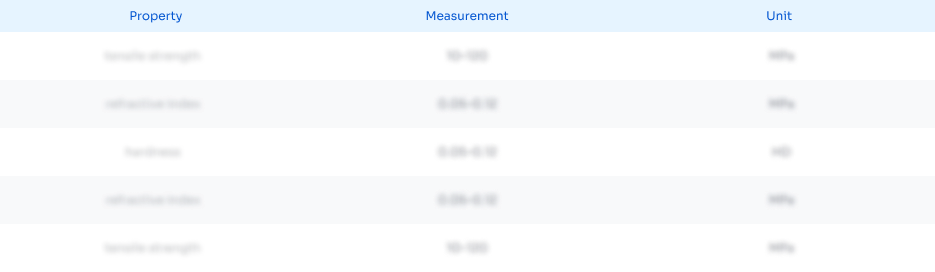
Abstract
Description
Claims
Application Information

- R&D
- Intellectual Property
- Life Sciences
- Materials
- Tech Scout
- Unparalleled Data Quality
- Higher Quality Content
- 60% Fewer Hallucinations
Browse by: Latest US Patents, China's latest patents, Technical Efficacy Thesaurus, Application Domain, Technology Topic, Popular Technical Reports.
© 2025 PatSnap. All rights reserved.Legal|Privacy policy|Modern Slavery Act Transparency Statement|Sitemap|About US| Contact US: help@patsnap.com