Winding equipment
A technology of winding equipment and equipment racks, which is applied in the direction of electrical components, inductance/transformer/magnet manufacturing, circuits, etc., can solve problems such as the flatness of easily damaged hollow coils, reduce coil production efficiency, and unimproved technical problems, and achieve shortening The length of the waste wire, the design and practicality, and the effect of improving the degree of mechanical automation
- Summary
- Abstract
- Description
- Claims
- Application Information
AI Technical Summary
Problems solved by technology
Method used
Image
Examples
Embodiment 1
[0038] like figure 1 As shown, the winding equipment includes an equipment rack 1, the equipment rack 1 is a cabinet structure and a U-shaped base 14 is provided on the equipment rack 1, and a wire inlet mechanism located behind the U-shaped base 14 is also provided on the equipment rack 1 7.
[0039] The wire inlet mechanism 7 comprises a vertically arranged bracket 71, and a horizontal bar 72 is provided at the upper end of the bracket, and several pieces of vertically arranged and spaced wire inlet boards 73 are arranged on the horizontal rod 72, and on each wire inlet board 73 A number of discretely arranged wire feed wheels 74 are provided respectively, and the wires to be wound pass through the wire feed wheels 74 on each wire feed board 73 in turn. Of course, they may not pass through all of them. The wire feed can be carried out according to the actual wire feed requirements. the wiring.
[0040] Secondly, the U-shaped base 14 is also provided with a cable-dischargin...
Embodiment 2
[0065] The structure and principle of this embodiment are basically the same as that of Embodiment 1, so it will not be repeated here. The difference is that any one of the jig molds 12 is provided with a hollow space between the two jig molds 12. The coil a breaks away from the stripping mechanism 6 on the molding surface of the jig mold 12 .
PUM
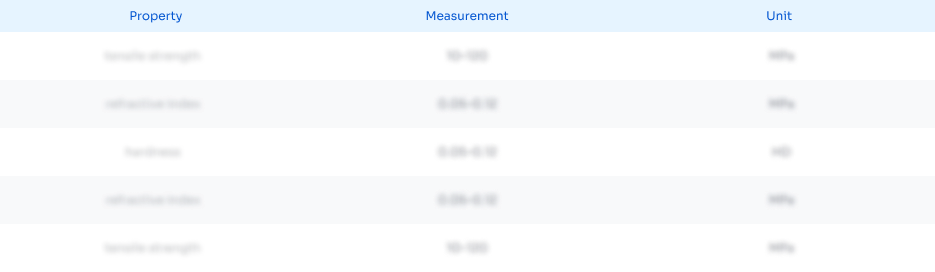
Abstract
Description
Claims
Application Information

- R&D Engineer
- R&D Manager
- IP Professional
- Industry Leading Data Capabilities
- Powerful AI technology
- Patent DNA Extraction
Browse by: Latest US Patents, China's latest patents, Technical Efficacy Thesaurus, Application Domain, Technology Topic, Popular Technical Reports.
© 2024 PatSnap. All rights reserved.Legal|Privacy policy|Modern Slavery Act Transparency Statement|Sitemap|About US| Contact US: help@patsnap.com