Controllable mechanism type stacking robot driven by electric push cylinders
A palletizing robot and electric push technology, applied in the field of machinery, can solve the problems of high precision, high speed and high load movement impact, high precision requirements for hydraulic parts manufacturing, hydraulic system is easily affected by environmental factors, etc., to achieve safety Reliable work, compact structure, smooth motion and increased reliability
- Summary
- Abstract
- Description
- Claims
- Application Information
AI Technical Summary
Problems solved by technology
Method used
Image
Examples
Embodiment 1
[0014] An electric push cylinder-driven controllable mechanism palletizing robot, including a base 8, a frame 5, a connecting rod 1, a connecting rod 2, a connecting rod 3, a connecting rod 4 4, a triangular connecting plate 6, and an electric push cylinder One 11, electric push cylinder two 12, electric push cylinder three 13 and execution terminal 7,
[0015] One end of connecting rod one 1 is connected to frame 5 through rotating pair one 101, and the other end of connecting rod one 1 is connected on connecting rod two 2 through rotating pair two 102.
[0016] One end of electric push cylinder one 11 is connected to connecting rod one 1 through rotating pair three 103, the other end of electric pushing cylinder one 11 is connected to one end of connecting rod two 2 through rotating pair four 104, and the other end of connecting rod two 2 is passed through rotating pair five 105 Connected to the execution terminal 7,
[0017] One end of the electric push cylinder two 12 is ...
PUM
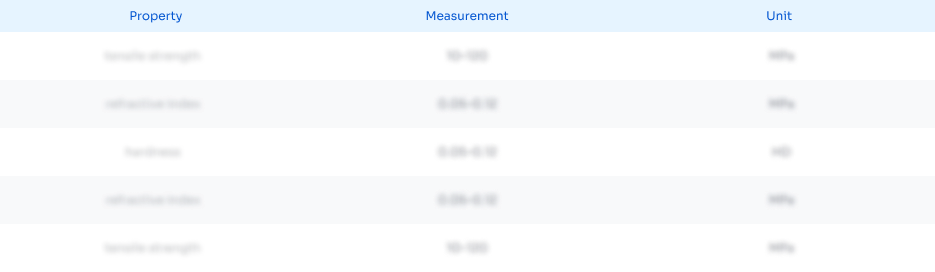
Abstract
Description
Claims
Application Information

- R&D Engineer
- R&D Manager
- IP Professional
- Industry Leading Data Capabilities
- Powerful AI technology
- Patent DNA Extraction
Browse by: Latest US Patents, China's latest patents, Technical Efficacy Thesaurus, Application Domain, Technology Topic, Popular Technical Reports.
© 2024 PatSnap. All rights reserved.Legal|Privacy policy|Modern Slavery Act Transparency Statement|Sitemap|About US| Contact US: help@patsnap.com