Small impeller mode testing method based on exciting point optimization and vibration measurement with laser
A laser vibration measurement and excitation point technology, used in vibration testing, machine/structural component testing, measuring devices, etc., can solve problems such as low test accuracy, achieve a wide modal measurement range, and display the mode shape results clearly and intuitively. The effect of high natural frequency accuracy
- Summary
- Abstract
- Description
- Claims
- Application Information
AI Technical Summary
Problems solved by technology
Method used
Image
Examples
Embodiment Construction
[0019] refer to Figure 1-3 . The specific steps of the small impeller modal test method based on excitation point optimization and laser vibration measurement in the present invention are as follows:
[0020] Establish the three-dimensional geometric model of the impeller in the UG modeling software, import it into the ANSYS software for mesh division, material properties, boundary conditions and load settings, establish a finite element model, and calculate the first 5 natural frequencies and mode shapes of the model . Import the mesh division and modal calculation results of the impeller disk model into the vibration and noise correlation analysis module in LMS Virtual. Possibly multiple modal frequencies.
[0021] The impeller modal laser vibration measurement test was carried out under the guidance of the excitation point optimization results. In order to enhance the reflected light intensity of the laser test, reflective paper was pasted on the impeller disk, and a c...
PUM
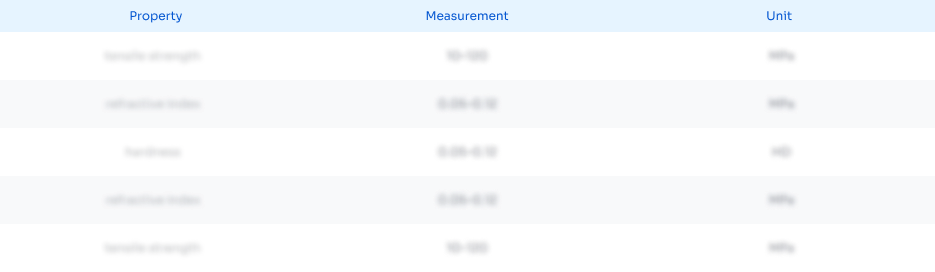
Abstract
Description
Claims
Application Information

- R&D
- Intellectual Property
- Life Sciences
- Materials
- Tech Scout
- Unparalleled Data Quality
- Higher Quality Content
- 60% Fewer Hallucinations
Browse by: Latest US Patents, China's latest patents, Technical Efficacy Thesaurus, Application Domain, Technology Topic, Popular Technical Reports.
© 2025 PatSnap. All rights reserved.Legal|Privacy policy|Modern Slavery Act Transparency Statement|Sitemap|About US| Contact US: help@patsnap.com