A fluid hydrodynamic bearing
A fluid dynamic pressure bearing and fluid dynamic pressure technology, applied in sliding contact bearings, bearings, bearings in rotating motion, etc., can solve problems such as insufficient load capacity and insufficient rigidity, and achieve high rotational accuracy and load capacity, and improved quietness. Effect
- Summary
- Abstract
- Description
- Claims
- Application Information
AI Technical Summary
Problems solved by technology
Method used
Image
Examples
Embodiment Construction
[0050] Hereinafter, examples of the present invention will be described with reference to the drawings, but the present invention is not limited to these examples.
[0051] refer to Figure 1-19 , an embodiment of the fluid dynamic bearing of the present invention and an embodiment of the cam mechanism constituting the fluid dynamic bearing of the present invention will be described.
[0052] figure 1 A cross-sectional view of the fluid dynamic pressure bearing 101 is shown. The fluid dynamic pressure bearing 101 includes a shaft member 104, an outer ring portion 102 rotatable along an outer peripheral surface 107 of the shaft member 104, and a diameter is provided between the outer peripheral surface 107 of the shaft member 104 and the inner peripheral surface 120 of the outer ring portion 102. To the gap 103. exist figure 1 Among them, the fluid dynamic pressure bearing 101 further includes: an insertion portion 105 for fitting the fluid dynamic pressure bearing 101 to a...
PUM
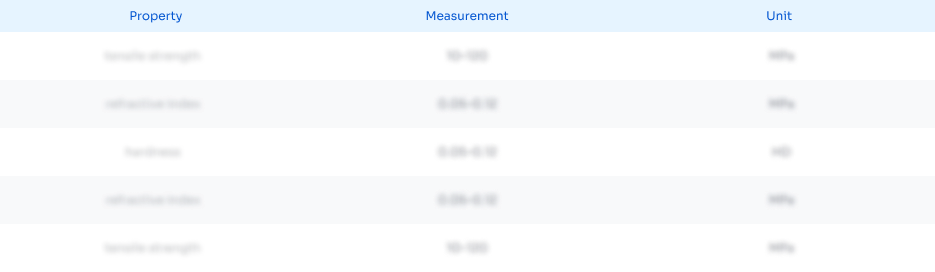
Abstract
Description
Claims
Application Information

- R&D
- Intellectual Property
- Life Sciences
- Materials
- Tech Scout
- Unparalleled Data Quality
- Higher Quality Content
- 60% Fewer Hallucinations
Browse by: Latest US Patents, China's latest patents, Technical Efficacy Thesaurus, Application Domain, Technology Topic, Popular Technical Reports.
© 2025 PatSnap. All rights reserved.Legal|Privacy policy|Modern Slavery Act Transparency Statement|Sitemap|About US| Contact US: help@patsnap.com