Fixed point mechanism
A component and shaft structure technology, applied in the field of fixed point mechanism
- Summary
- Abstract
- Description
- Claims
- Application Information
AI Technical Summary
Problems solved by technology
Method used
Image
Examples
Embodiment 1
[0105] Please refer to figure 1 , which is a schematic diagram of the principle of the fixed point mechanism in Embodiment 1 of the present invention. Such as figure 1 As shown, the fixed point mechanism 1 includes: a driving component, a driven component and a transmission component. Specifically, the active component includes: a first link member 100, a second link member 101, a third link member 102, a fourth link member 103 and a slider device 110, wherein the first link The first end (the lower end here) of the member 100 forms a rotational connection with the first end (the proximal end here) of the second link member 101 through the first rotating shaft structure 120, and the second link member 101 The second end (the distal end here) is rotationally connected with the slider device 110 through the second rotating shaft structure 121, the third link member 102 forms a sliding connection with the slider device 110, and the first The three link members 102 pass through...
Embodiment 2
[0119] Please refer to image 3 , which is a schematic diagram of the principle of the fixed point mechanism in Embodiment 2 of the present invention. Such as image 3 As shown, the fixed point mechanism 2 includes: a driving component, a driven component and a transmission component. Specifically, the active component includes: a first link member 200, a second link member 201, a third link member 202, a fourth link member 203 and a slider device 210, wherein the first link The first end (the lower end here) of the member 200 forms a rotational connection with the first end (the proximal end here) of the second link member 201 through the first rotating shaft structure 220, and the second link member 201 The second end (the distal end here) forms a rotational connection with the slider device 210 through the second shaft structure 221, the third link member 202 forms a sliding connection with the slider device 210, and the third The connecting rod member 202 passes through...
Embodiment 3
[0132] Please refer to Figure 5 , which is a schematic diagram of the principle of the fixed point mechanism in Embodiment 3 of the present invention. Such as Figure 5 As shown, the fixed point mechanism 3 includes: a driving component, a driven component and a transmission component. Specifically, the active component includes: a first link member 300, a second link member 301, a third link member 302, a fourth link member 303 and a slider device 310, wherein the first link The first end (the lower end here) of the member 300 forms a rotational connection with the first end (the proximal end here) of the second link member 301 through the first rotating shaft structure 320, and the second link member 301 The second end (the distal end here) forms a rotational connection with the slider device 310 through the second rotating shaft structure 321, the third link member 302 forms a sliding connection with the slider device 310, and the The third connecting rod member 302 pas...
PUM
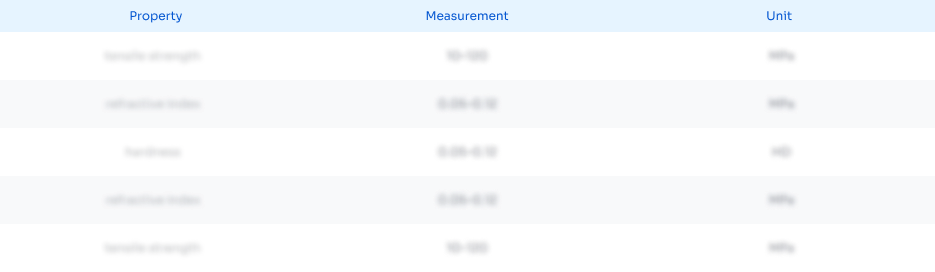
Abstract
Description
Claims
Application Information

- R&D
- Intellectual Property
- Life Sciences
- Materials
- Tech Scout
- Unparalleled Data Quality
- Higher Quality Content
- 60% Fewer Hallucinations
Browse by: Latest US Patents, China's latest patents, Technical Efficacy Thesaurus, Application Domain, Technology Topic, Popular Technical Reports.
© 2025 PatSnap. All rights reserved.Legal|Privacy policy|Modern Slavery Act Transparency Statement|Sitemap|About US| Contact US: help@patsnap.com