Efficient waste heat utilization system for coal-to-liquids technology condensate
A technology for process condensate and coal-to-oil, which is applied in the field of coal-to-oil to achieve the effects of obvious energy saving and emission reduction, wide application prospects and improved comprehensive utilization efficiency
- Summary
- Abstract
- Description
- Claims
- Application Information
AI Technical Summary
Problems solved by technology
Method used
Image
Examples
Embodiment 1
[0018] see figure 2 , the present invention discloses a high-efficiency utilization system for condensate waste heat in coal-to-liquids process. The system includes a two-stage waste heat utilization system. The first-stage waste heat utilization system adopts a flash heat recovery system to recover flash steam, and the second-stage waste heat utilization system The system uses the Organic Rankine Cycle (ORC cycle) to generate electricity.
[0019] The first-stage waste heat utilization system is a flash heat recovery system, including a flash tank 6 and a steam heat recovery device 7, and the high-temperature process condensate (usually at a temperature of 110-130°C) is connected to the flash tank through the process condensate interface 11 Inlet 6, saturated steam is flashed out, and the flash steam is connected to the steam heat recovery device 7 from the top of the flash tank 6 for use in other processes, and the low-temperature condensate at the outlet of the flash heat ...
Embodiment 2
[0022] see image 3 , The difference between Embodiment 2 and Embodiment 1 is that in this embodiment, the steam heat recovery and utilization device of the first-stage waste heat utilization system is a steam condenser 8, and the high-temperature process condensate (usually at a temperature of 110-130° C.) passes through the process The condensate interface 11 is connected to the inlet of the flash tank 6, and saturated steam is flashed out. The flash steam enters the steam condenser 8 from the top of the flash tank 6 to condense and release heat, which is used for heating the process cold medium. After the condensate is mixed with the condensate at the outlet of the flash tank (at a temperature of 75°C to 100°C), it enters the second-stage waste heat utilization system.
Embodiment 3
[0024] see Figure 4 The difference between Embodiment 3 and Embodiment 1 is that in this embodiment, the steam heat recovery and utilization device of the first-stage waste heat utilization system is a steam jet heat pump 9, and the high-temperature process condensate (usually at a temperature of 110-130°C) passes through the process The condensate interface 11 is connected to the inlet of the flash tank 6 to flash saturated steam. The flash steam enters the steam injection heat pump 9 from the top of the flash tank 6 and mixes with the high-temperature and high-pressure driving steam to form usable steam. The flash tank 6. The low-temperature condensate (with a temperature of 75°C to 100°C) at the outlet enters the second-stage waste heat utilization system.
PUM
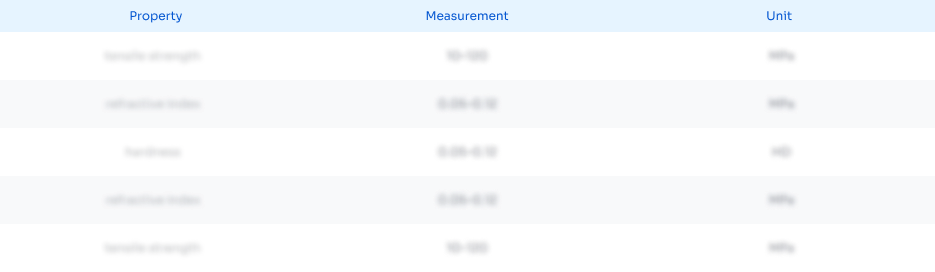
Abstract
Description
Claims
Application Information

- Generate Ideas
- Intellectual Property
- Life Sciences
- Materials
- Tech Scout
- Unparalleled Data Quality
- Higher Quality Content
- 60% Fewer Hallucinations
Browse by: Latest US Patents, China's latest patents, Technical Efficacy Thesaurus, Application Domain, Technology Topic, Popular Technical Reports.
© 2025 PatSnap. All rights reserved.Legal|Privacy policy|Modern Slavery Act Transparency Statement|Sitemap|About US| Contact US: help@patsnap.com