Through shaft type tension sensor
A technology of tension sensor and shaft threading, applied in tension measurement, instrument, measurement force, etc., can solve the problems of poor accuracy, high maintenance cost, short long-term service life, etc., and achieve long service life, high precision and good stability. Effect
- Summary
- Abstract
- Description
- Claims
- Application Information
AI Technical Summary
Problems solved by technology
Method used
Image
Examples
no. 1 example
[0048] see figure 1 — Figure 4 , The sensor includes a shell 1, a circular bearing frame 2, a self-aligning bearing 3, a strain beam 4, a control circuit, an output interface 5, an inner plate 7, and an outer plate 8.
[0049] The housing 1 is formed by connecting a circular inner ring 1c and an outer ring 1b coaxially. The axial thickness of the inner ring 1c is smaller than the axial thickness of the outer ring 1b, and the inner ring 1c is located in the axial middle area of the outer ring 1b. Two recesses 1f are formed on both sides in the axial direction between the inner ring 1c and the outer ring 1b, and the two recesses 1f are the inside of the housing 1 .
[0050] The bearing frame 2 is coaxially located in the inner ring 1c with a gap between them, the gap is 3-5 mm, and the axial thickness of the bearing frame 2 is between the axial thickness of the inner ring 1c and the axial thickness of the outer ring 1b. Between the thickness, the self-aligning bearing 3 is ...
no. 2 example
[0065] see Figure 5 , compared with the first embodiment, the second embodiment only has a different cross-sectional shape of the protrusion 6 along the radial direction of the bearing frame 2 .
[0066] For the cross-sectional shape of the projection 6 along the radial direction of the bearing frame 2 is a large semicircle, the cylindrical surface of the large semicircle is in an overhanging state, and the radial extension length of the large semicircle is equal to the radial extension length of the strain beam 4 The ratio is (0.5-0.7):1, and the ratio of the width of the large semicircle to the width of the strain beam 4 is (3.1-3.3):1.
no. 3 example
[0068] see Figure 6 , compared with the first embodiment, only the cross-sectional shape of the protrusion 6 along the radial direction of the bearing frame 2 is different in the third embodiment.
[0069] For the cross-sectional shape of the projection 6 along the radial direction of the bearing frame 2 is a half-waist circle, the cylindrical surface of the half-waist circle is in an overhanging state, and the radial extension length of the half-waist circle is the same as that of the strain beam 4 The ratio of the radial extension length of the beam is (0.8-1):1, and the ratio of the width of the half girdle to the width of the strain beam 4 is (3.1-3.3):1.
PUM
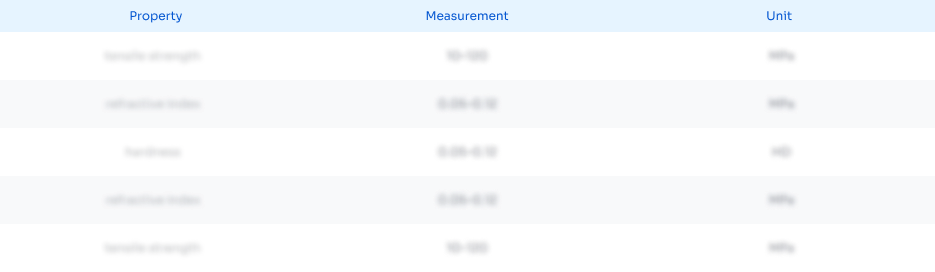
Abstract
Description
Claims
Application Information

- R&D
- Intellectual Property
- Life Sciences
- Materials
- Tech Scout
- Unparalleled Data Quality
- Higher Quality Content
- 60% Fewer Hallucinations
Browse by: Latest US Patents, China's latest patents, Technical Efficacy Thesaurus, Application Domain, Technology Topic, Popular Technical Reports.
© 2025 PatSnap. All rights reserved.Legal|Privacy policy|Modern Slavery Act Transparency Statement|Sitemap|About US| Contact US: help@patsnap.com