A kind of anti-wind ball bearing
A ball bearing and bearing technology, applied in the field of bridge structure, can solve the problems of affecting the bearing capacity, tension and compression vibration fatigue of the central connecting rod, and the reduction of the bearing area of the spherical crown steel lining plate, so as to achieve long service life and durability. The effect of good performance and reliable mosaic connection
- Summary
- Abstract
- Description
- Claims
- Application Information
AI Technical Summary
Problems solved by technology
Method used
Image
Examples
Embodiment 1
[0046]A wind-resistant spherical bearing, comprising a bearing top plate 1, a bearing bottom plate 2, a middle backing plate 5 and a liner, the liner is a spherical steel liner, including a convex spherical steel liner 7 and a concave spherical steel liner plate 9, the middle backing plate 5, the convex spherical steel liner 7 and the concave spherical steel liner 9 are sequentially installed in the pelvic cavity of the support bottom plate 2, and one side of the convex spherical steel liner slides with the middle backing plate 5 The matching flat side, and the other side is a convex spherical surface; one side of the concave spherical steel liner is a flat side that slides with the top plate of the support, and the other side is a concave spherical surface that slides with the convex spherical surface of the convex spherical steel liner , the convex spherical steel liner 7 and the concave spherical steel liner constitute the rotation mechanism of the support, which realizes th...
Embodiment 2
[0057] A wind-resistant ball-type support, the structure of which is basically the same as that of Embodiment 1, the difference is that the number of the butterfly springs is 3, and there are 3 corresponding ones at the bottom of the pelvic cavity on the base plate of the support. In the groove Ⅰ21 inlaid with the Belleville spring (refer to the attached Figure 5 ).
Embodiment 3
[0059] A wind-resistant ball bearing, the structure of which is basically the same as that of Embodiment 1, the difference is that the number of the butterfly springs is 4, and the bottom of the pelvis of the bearing is provided with 4 corresponding ones for In the groove Ⅰ21 inlaid with the Belleville spring (refer to the attached Figure 6 ).
PUM
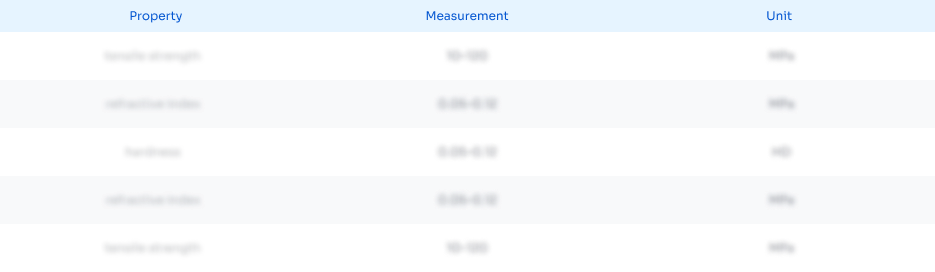
Abstract
Description
Claims
Application Information

- Generate Ideas
- Intellectual Property
- Life Sciences
- Materials
- Tech Scout
- Unparalleled Data Quality
- Higher Quality Content
- 60% Fewer Hallucinations
Browse by: Latest US Patents, China's latest patents, Technical Efficacy Thesaurus, Application Domain, Technology Topic, Popular Technical Reports.
© 2025 PatSnap. All rights reserved.Legal|Privacy policy|Modern Slavery Act Transparency Statement|Sitemap|About US| Contact US: help@patsnap.com