A flapping-wing aircraft capable of vertical take-off and landing and its flight control method
A flapping-wing aircraft and vertical take-off and landing technology, applied in the field of aircraft, can solve problems such as the inability to meet the requirements of large lift, difficulty in increasing the flapping frequency, and small lift of flexible blades, and achieve compact structure, high flapping frequency, flapping wings, etc. Mechanism Simple Effect
- Summary
- Abstract
- Description
- Claims
- Application Information
AI Technical Summary
Problems solved by technology
Method used
Image
Examples
Embodiment Construction
[0024] The present invention will be further described below in conjunction with accompanying drawing.
[0025] The invention provides a vertical take-off and landing flapping wing aircraft, such as figure 1 , figure 2 As shown, it includes the main load-bearing structure 1 of the fuselage and four sets of independent flapping wing mechanisms with the same structure. The main load-bearing structure 1 of the fuselage has a landing gear below. When the aircraft is placed on a horizontal plane, The bottom surface of the main bearing structure 1 of the fuselage is parallel to the horizontal plane. Described four sets of flapping wing mechanisms are distributed on the four corners of the main load-bearing structure 1 of the fuselage, and each set of flapping wing mechanisms is as follows: image 3 Shown, all comprise blade 2, rocking bar 3, connecting rod 4, crank 5 and motor 6. The blade 2 is as Figure 5 As shown, the first hinge is connected to the rocker 3, and the axis of...
PUM
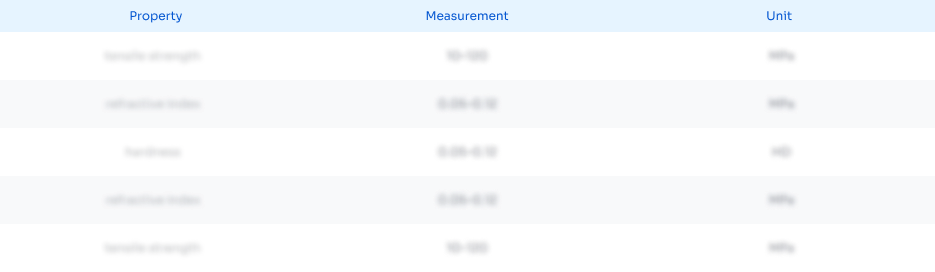
Abstract
Description
Claims
Application Information

- Generate Ideas
- Intellectual Property
- Life Sciences
- Materials
- Tech Scout
- Unparalleled Data Quality
- Higher Quality Content
- 60% Fewer Hallucinations
Browse by: Latest US Patents, China's latest patents, Technical Efficacy Thesaurus, Application Domain, Technology Topic, Popular Technical Reports.
© 2025 PatSnap. All rights reserved.Legal|Privacy policy|Modern Slavery Act Transparency Statement|Sitemap|About US| Contact US: help@patsnap.com