Numerically-controlled machine tool spindle thermal extension error real-time compensation method
A technology of real-time compensation and CNC machine tools, applied in the direction of program control, computer control, general control system, etc., can solve problems such as real-time compensation that does not involve the thermal elongation error of the spindle, and improve the adaptability of working conditions and the robustness of the model Strong, reduced-complexity effects
- Summary
- Abstract
- Description
- Claims
- Application Information
AI Technical Summary
Problems solved by technology
Method used
Image
Examples
Embodiment Construction
[0027] The implementation process of the present invention will be described in detail below in conjunction with the accompanying drawings and technical solutions.
[0028]The machine tool selected in the embodiment is a precision vertical machining center, the maximum spindle speed is 6000r / min, the axis of the spindle is consistent with the Z axis, and the positioning accuracy of the linear axis is 0.01mm. Two temperature sensors Pt100, measuring range 10℃~100℃, output voltage signal 0V~10V; displacement sensor ZX-EM, measuring range 2mm, linearity ±0.5%, output voltage signal -5V~+5V. The ambient temperature is 18°C to 23°C.
[0029] The real-time compensation process for the thermal elongation error of the CNC machine tool spindle is as follows: figure 1 As shown, the specific steps of the method are as follows:
[0030] In the first step, the spindle temperature sensor S is respectively arranged near the front bearing of the spindle 3 and on the spindle motor 1 1 and...
PUM
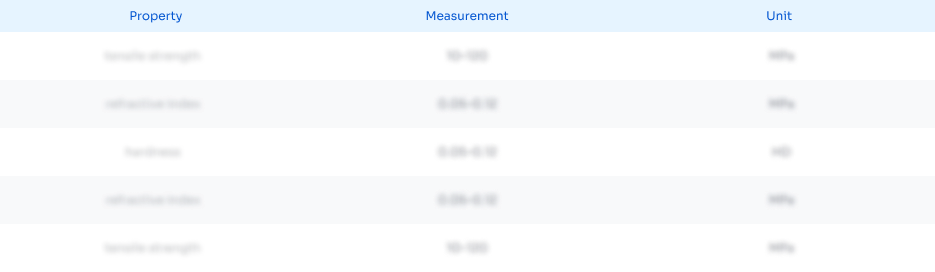
Abstract
Description
Claims
Application Information

- Generate Ideas
- Intellectual Property
- Life Sciences
- Materials
- Tech Scout
- Unparalleled Data Quality
- Higher Quality Content
- 60% Fewer Hallucinations
Browse by: Latest US Patents, China's latest patents, Technical Efficacy Thesaurus, Application Domain, Technology Topic, Popular Technical Reports.
© 2025 PatSnap. All rights reserved.Legal|Privacy policy|Modern Slavery Act Transparency Statement|Sitemap|About US| Contact US: help@patsnap.com