Furnace slag granulation system with automatic cleaning function
An automatic cleaning and granulation technology, applied in the improvement of process efficiency, recycling technology and other directions, can solve the problems of large and complex equipment, high investment and operating costs, and difficulty in coordinating wind speed and air volume, so as to reduce investment and operating costs. Uniform particle size and ideal granulation effect
- Summary
- Abstract
- Description
- Claims
- Application Information
AI Technical Summary
Problems solved by technology
Method used
Image
Examples
Embodiment Construction
[0025] The present invention will be further described in detail below in conjunction with the accompanying drawings and through specific embodiments. The following embodiments are only descriptive, not restrictive, and cannot limit the protection scope of the present invention.
[0026] In this embodiment, a slag granulation system with an automatic cleaning function can receive high-temperature slag and perform granulation treatment on the slag, and the treated slag can be used for secondary use.
[0027] Such as figure 1 As shown, the granulation system includes a slag tank 1 , a first roll 2 , a second roll 3 , a first scraper 4 , a second scraper 5 , and a granulation device 6 .
[0028] The slag tank 1 is used to receive high-temperature slag. The slag tank 1 includes the straight section 7 of the slag tank and the inclined section 8 of the slag tank. With an opening, the straight section 7 of the slag tank can buffer the falling of slag, reduce the impact of high-tempe...
PUM
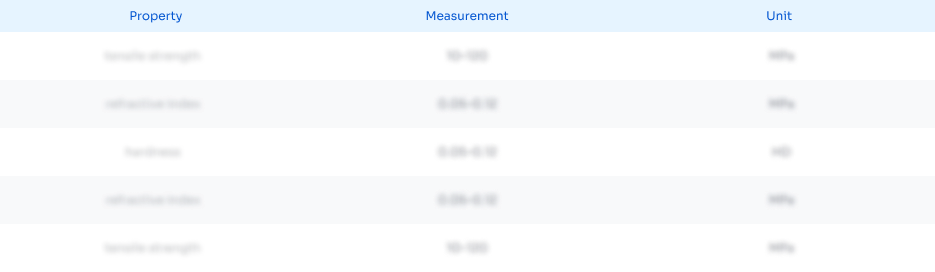
Abstract
Description
Claims
Application Information

- R&D Engineer
- R&D Manager
- IP Professional
- Industry Leading Data Capabilities
- Powerful AI technology
- Patent DNA Extraction
Browse by: Latest US Patents, China's latest patents, Technical Efficacy Thesaurus, Application Domain, Technology Topic, Popular Technical Reports.
© 2024 PatSnap. All rights reserved.Legal|Privacy policy|Modern Slavery Act Transparency Statement|Sitemap|About US| Contact US: help@patsnap.com