Production technology for foaming car seat synthetic cotton
An automobile seat and production process technology, which is applied in the field of foamed foam production technology, can solve the problems of increased storage, management, experiment and other expenses, poor foaming, low yield of foamed foam, etc. Comfort, reduced management, improved productivity
- Summary
- Abstract
- Description
- Claims
- Application Information
AI Technical Summary
Problems solved by technology
Method used
Examples
specific Embodiment approach
[0015] A kind of production technology of automobile seat composite foaming, concrete process is as follows:
[0016] a. Send the raw material combination polyether and isocyanate to the pumping room respectively, and use the pump to pump the combined polyether and isocyanate into their respective spare storage tanks. The air pressure of the spare storage tanks is set at 2-3kg / m²;
[0017] b. Automatically send the combined polyether and isocyanate of the spare storage tank into the respective working storage tanks through the automatic feeding system, and then inject the combined polyether and isocyanate into the filling gun head from the respective working storage pipes through the high-pressure filling machine, Mixing by filling the gun head; wherein: the mass ratio of the combined polyether and isocyanate is 100:34-48; the temperature of the working storage tank of the combined polyether is controlled at 23±3°C, and the working storage tank of the isocyanate The temperatur...
PUM
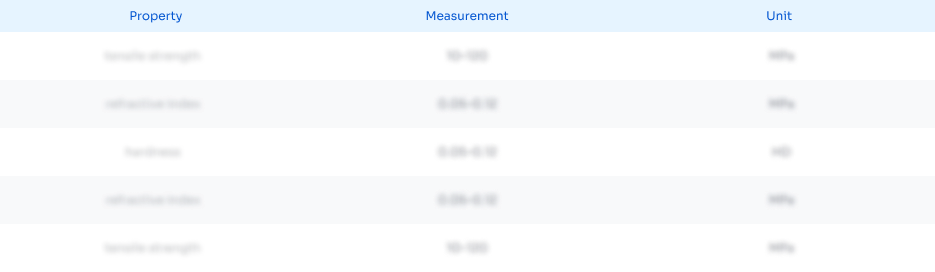
Abstract
Description
Claims
Application Information

- R&D
- Intellectual Property
- Life Sciences
- Materials
- Tech Scout
- Unparalleled Data Quality
- Higher Quality Content
- 60% Fewer Hallucinations
Browse by: Latest US Patents, China's latest patents, Technical Efficacy Thesaurus, Application Domain, Technology Topic, Popular Technical Reports.
© 2025 PatSnap. All rights reserved.Legal|Privacy policy|Modern Slavery Act Transparency Statement|Sitemap|About US| Contact US: help@patsnap.com