Radial magnetic bearing and sensor bracket split structure
A sensor bracket and split structure technology, applied in the direction of magnetic bearings, bearings, bearing components, etc., can solve problems such as high maintenance costs, production delays, and complicated maintenance processes, so as to reduce maintenance costs and time, facilitate production arrangements, The effect of simplifying the control procedure
- Summary
- Abstract
- Description
- Claims
- Application Information
AI Technical Summary
Problems solved by technology
Method used
Image
Examples
Example Embodiment
[0026] The present invention will be further described below in conjunction with the accompanying drawings.
[0027] like figure 1 As shown in the figure, a radial magnetic bearing and a sensor bracket split structure of the present invention includes a radial magnetic bearing 1, a displacement sensor 2, a magnetic bearing bracket 3 and a sensor bracket 4, and the magnetic bearing bracket 3 and the sensor bracket 4 are both annular structures , the sensor bracket 4 is arranged in the magnetic bearing bracket 3 coaxially, and there is an interference fit between the two. The magnetic pole of the radial magnetic bearing 1 is fixed in the magnetic bearing bracket 3 , and the displacement sensor 2 is installed on the inner ring surface of the sensor bracket 4 .
[0028] The magnetic bearing bracket 3 is provided with a stepped surface 31 for mounting the sensor bracket 4 .
[0029] The inner annular surface A of the radial magnetic bearing 1 and the inner circumferential surface...
PUM
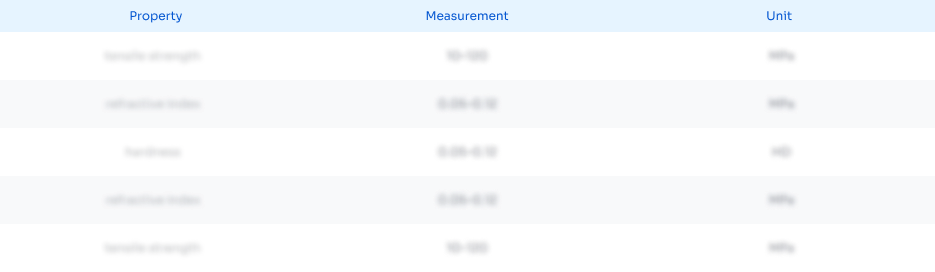
Abstract
Description
Claims
Application Information

- R&D
- Intellectual Property
- Life Sciences
- Materials
- Tech Scout
- Unparalleled Data Quality
- Higher Quality Content
- 60% Fewer Hallucinations
Browse by: Latest US Patents, China's latest patents, Technical Efficacy Thesaurus, Application Domain, Technology Topic, Popular Technical Reports.
© 2025 PatSnap. All rights reserved.Legal|Privacy policy|Modern Slavery Act Transparency Statement|Sitemap|About US| Contact US: help@patsnap.com