Rubber for swing arm liner bushings and preparation method for rubber
A rubber and viscose technology is applied in the field of rubber and its preparation for swing arm bushings, which can solve the problems of short service life and poor use stability.
- Summary
- Abstract
- Description
- Claims
- Application Information
AI Technical Summary
Problems solved by technology
Method used
Image
Examples
Embodiment 1
[0027] A method for preparing rubber for a swing arm bushing, which includes the following steps: 1) Rubber mixing: First, each component is weighed according to the following mass percentages: constant viscose 30%, butadiene rubber 20%, and filler: 40%, plasticizer 2%, accelerator 3%, antioxidant 4010NA 2%, antioxidant MB 0.5%, antioxidant-1178 2.5%; then leave it for 48 hours after plasticizing the raw rubber; Mix the other components except the accelerator; leave for 48 hours after mixing and then add the accelerator for mixing; 2) Vulcanization: the vulcanization temperature is 165°C, the vulcanization time is 9 minutes, and the clamping pressure is 15 MPa.
Embodiment 2
[0029] A method for preparing rubber for a swing arm bushing, which includes the following steps: 1) Rubber mixing: First, each component is weighed according to the following mass percentages: 10% for constant viscose, 40% for butadiene rubber, and filler: 40%, plasticizer is 3.5%, accelerator is 1%, antioxidant 4010NA is 2%, antioxidant MB is 1.5%, antioxidant-1178 is 2%; then the raw rubber is plasticized and left for 22 hours; then with Mixing of other components except accelerator; after mixing, stop for 23 hours and then add accelerator for mixing; 2) Vulcanization: vulcanization temperature is 155℃, vulcanization time is 14 minutes, and clamping pressure is 25 MPa.
Embodiment 3
[0031] A method for preparing rubber for swing arm bushings, which includes the following steps: 1) Rubber mixing: First, each component is weighed according to the following mass percentages: 20% for constant viscose, 35% for butadiene rubber, and filler: 35%, plasticizer 3%, accelerator 2%, antioxidant 4010NA 1%, antioxidant MB 1%, antioxidant-1178 3%; then leave it for 24 hours after the raw rubber is plasticized; Mix the other components except the accelerator; leave for 24 hours after mixing and then add the accelerator for mixing; 2) Vulcanization: the vulcanization temperature is 160°C, the vulcanization time is 12 minutes, and the clamping pressure is 20 MPa.
PUM
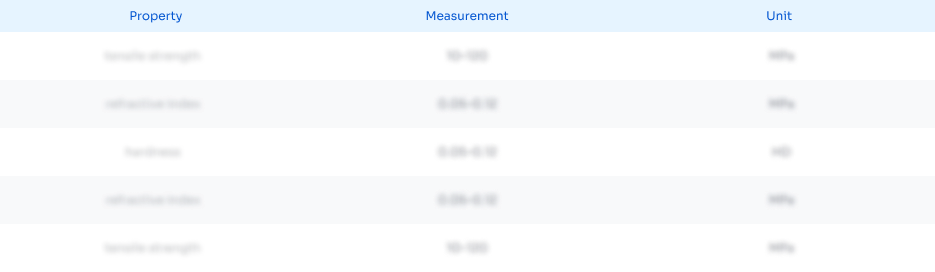
Abstract
Description
Claims
Application Information

- R&D
- Intellectual Property
- Life Sciences
- Materials
- Tech Scout
- Unparalleled Data Quality
- Higher Quality Content
- 60% Fewer Hallucinations
Browse by: Latest US Patents, China's latest patents, Technical Efficacy Thesaurus, Application Domain, Technology Topic, Popular Technical Reports.
© 2025 PatSnap. All rights reserved.Legal|Privacy policy|Modern Slavery Act Transparency Statement|Sitemap|About US| Contact US: help@patsnap.com