Shaping and punching device and method for shaping and punching oil storage cylinder steering knuckle bracket
A steering knuckle bracket and punching device technology, which is applied to punching tools, pushing equipment, manufacturing tools, etc., can solve problems such as affecting product quality and production efficiency, large fluctuations in punching size, and inconsistent positioning benchmarks, avoiding positioning Unstable, good product quality, high precision effect
- Summary
- Abstract
- Description
- Claims
- Application Information
AI Technical Summary
Problems solved by technology
Method used
Image
Examples
Embodiment 1
[0085] A shaping and punching device, including a control unit I and a working unit II, the working unit includes a core device 1 installed on a workbench, a longitudinal positioning mechanism 2, a clamping shaping mechanism and a punching mechanism,
[0086]The control unit is used to control the longitudinal positioning mechanism, the clamping and shaping mechanism and the punching mechanism to complete the positioning, clamping and shaping and punching work according to the set procedure, and the mold core device is used to provide the mold core corresponding to the opening of the steering knuckle bracket Easy to shape and punch,
[0087] The longitudinal positioning mechanism is used to tighten the oil storage tank assembly and determine the front and rear positions of the steering knuckle bracket. The clamping and shaping mechanism is used to clamp the oil storage tank assembly to determine the punching position of the steering knuckle bracket and shape the steering knuckl...
Embodiment 2
[0103] A method for shaping and punching the steering knuckle bracket of the oil storage tank, which is a method of shaping and punching the steering knuckle bracket of the oil storage tank by using the shaping and punching device described in Embodiment 1, comprising the following steps:
[0104] (1) Assemble the shaping and punching device
[0105] S11: install the mold core support plate: longitudinally install the mold core support plate 11 to the middle of the workbench by screws;
[0106] S12: Install the hydraulic device: install the guide rail 4 on the worktables on the left and right sides of the core device, and install the hydraulic device on the guide rail through the slide rail 54 at the bottom of the hydraulic device 5;
[0107] S13: Assemble the clamping and shaping device and the punching device:
[0108] First, press-fit two guide rods 14 into the guide rod mounting holes 122 of the mold core mounting plate 12, and sequentially insert the clamping arms 61, pu...
PUM
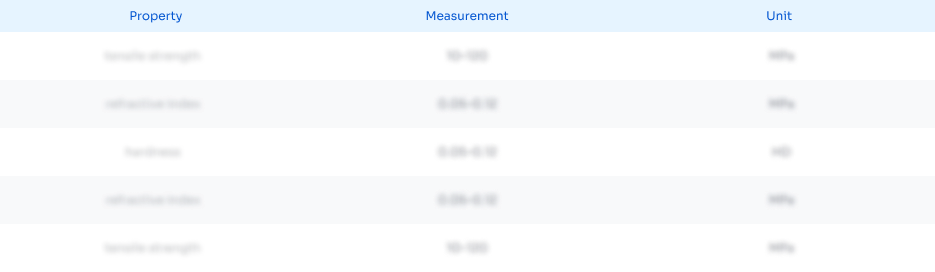
Abstract
Description
Claims
Application Information

- R&D
- Intellectual Property
- Life Sciences
- Materials
- Tech Scout
- Unparalleled Data Quality
- Higher Quality Content
- 60% Fewer Hallucinations
Browse by: Latest US Patents, China's latest patents, Technical Efficacy Thesaurus, Application Domain, Technology Topic, Popular Technical Reports.
© 2025 PatSnap. All rights reserved.Legal|Privacy policy|Modern Slavery Act Transparency Statement|Sitemap|About US| Contact US: help@patsnap.com