Vibration energy collector
A vibration energy harvesting, mass block technology, applied in the direction of generator/motor, piezoelectric effect/electrostrictive or magnetostrictive motor, electrical components, etc., can solve the problem of low frequency point energy density, unfavorable energy harvesting, resonance Problems such as narrow bandwidth at frequency
- Summary
- Abstract
- Description
- Claims
- Application Information
AI Technical Summary
Problems solved by technology
Method used
Image
Examples
Embodiment 1
[0023] like figure 1 As shown, the vibration energy harvester described in this embodiment includes a piezoelectric cantilever beam 1 and a mass block 2, and the piezoelectric cantilever beam 1 includes a horizontally arranged main beam 10 and a plurality of longitudinally arranged first subbeams 11 and a plurality of second secondary beams 12 arranged longitudinally, one end of the main beam 10 is a fixed end, the other end of the main beam 10 is a free end, and the mass block 2 is fixed on the free end of the main beam 10, A plurality of the first sub-beams 11 are arranged at intervals and fixed on one side of the main beam 10 , and a plurality of the second sub-beams 12 are arranged at intervals and fixed on the other side of the main beam 10 .
[0024] The above-mentioned vibration energy harvester applies an external force to the piezoelectric cantilever beam 1, which will cause the positive piezoelectric effect of the piezoelectric cantilever beam 1 to generate current. ...
Embodiment 2
[0030] The difference between the vibration energy harvester described in the second embodiment and the vibration energy harvester described in the embodiment is that in the second embodiment, there are two mass blocks 2, and the two mass blocks 2 are respectively fixed on the installation beam 13 The two ends of the piezoelectric cantilever beam 1 are thus increased to generate more electric energy.
[0031] The number of the first sub-beams 11 is equal to the number of the second sub-beams 12, both of which are five. It should be noted that the number of the first sub-beams 11 is preferably 4-6, and the number of the second sub-beams 12 is preferably 4-6, so that there are enough resonant frequency points and the production difficulty is not high. high.
PUM
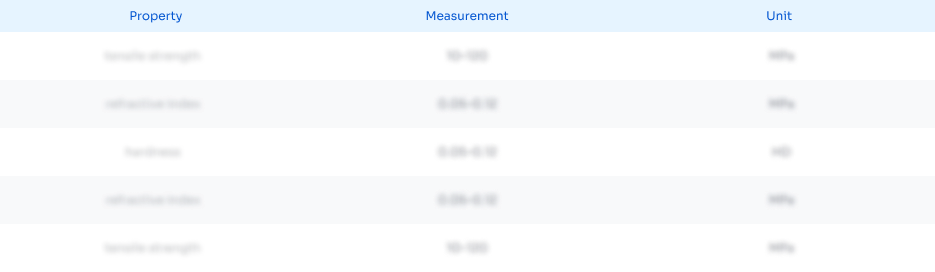
Abstract
Description
Claims
Application Information

- R&D
- Intellectual Property
- Life Sciences
- Materials
- Tech Scout
- Unparalleled Data Quality
- Higher Quality Content
- 60% Fewer Hallucinations
Browse by: Latest US Patents, China's latest patents, Technical Efficacy Thesaurus, Application Domain, Technology Topic, Popular Technical Reports.
© 2025 PatSnap. All rights reserved.Legal|Privacy policy|Modern Slavery Act Transparency Statement|Sitemap|About US| Contact US: help@patsnap.com