Rotating machinery shaft torsion vibration fault monitoring method under variable frequency speed regulation driving
A technology for shafting torsional vibration and rotating machinery, which is applied in the testing of mechanical parts, the testing of machine/structural parts, and measuring devices, etc. It can solve the problems of high requirements for equal parts, complex signal extraction and analysis, etc.
- Summary
- Abstract
- Description
- Claims
- Application Information
AI Technical Summary
Problems solved by technology
Method used
Image
Examples
Embodiment Construction
[0059] like figure 1 As shown, a method for monitoring torsional vibration faults of rotating machinery shafting driven by variable frequency speed regulation includes the following steps:
[0060] (1) Collect the three-phase stator current signal of the asynchronous motor i a i b i c ;
[0061] (2) Perform Park transformation and Clarke transformation on the three-phase stator current to obtain the d-axis and q-axis stator current i in the d-q coordinate system d i q ;
[0062] like figure 2 , 3 As shown in and 4, the Park transformation transforms the electromagnetic quantities such as current, voltage, and flux linkage in the three-phase a-b-c coordinate system into the stationary two-phase d-q coordinate system, ds and qs are the coordinate axes of the stationary d-q coordinate system, and the electromagnetic quantity transformation is as follows Formula (1) shows:
[0063] i d ...
PUM
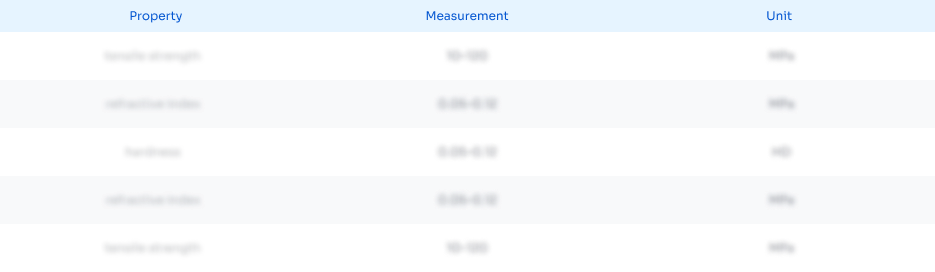
Abstract
Description
Claims
Application Information

- R&D
- Intellectual Property
- Life Sciences
- Materials
- Tech Scout
- Unparalleled Data Quality
- Higher Quality Content
- 60% Fewer Hallucinations
Browse by: Latest US Patents, China's latest patents, Technical Efficacy Thesaurus, Application Domain, Technology Topic, Popular Technical Reports.
© 2025 PatSnap. All rights reserved.Legal|Privacy policy|Modern Slavery Act Transparency Statement|Sitemap|About US| Contact US: help@patsnap.com