3D printing method for adding reinforcement-ratio based directional fibers into binding materials
A cementitious material and 3D printing technology, applied in the direction of additive processing, ceramic molding machine, manufacturing tools, etc., can solve the problems of molding time, low strength, unfavorable force of concrete structure, etc., and achieve the effect of reducing changes
- Summary
- Abstract
- Description
- Claims
- Application Information
AI Technical Summary
Problems solved by technology
Method used
Image
Examples
Embodiment 1
[0044] The 3D printing implementation method of increasing the directional fiber based on the reinforcement ratio in the cementitious material is characterized in that it includes the following steps:
[0045] Step 1, using double print head 3D printer technology (this technology already belongs to the prior art), to realize the lamellar layer printing of normal concrete by one of the print heads;
[0046] Step 2. When printing reaches the position where the steel bars need to be arranged, according to the required amount of fibers, another print head prints steel fibers perpendicular to the concrete printing surface;
[0047] Step 3. Insert the steel fiber into the printed concrete, and keep part of the length outside the layer;
[0048] Step 4. When printing the next layer of concrete, the above-mentioned exposed fiber part is covered by the newly printed concrete, and overlaps with the subsequent printed fibers in the length direction to ensure the transmission of the bondi...
Embodiment 2
[0053]Step 1. Use multiple print heads to realize that one of the print heads prints the flake layer of normal concrete (this technology can also be realized through existing existing technologies), and the other print heads print fibers;
[0054] Step 2. When printing to the position where the steel bars need to be arranged, according to the converted fiber amount, direction and position, different print heads insert fibers into the printed concrete in a specific direction;
[0055] Step 3: insert the fiber into the printed concrete, and keep part of the length outside the layer;
[0056] Step 4. When printing the next layer of concrete, the direction of travel of the printing head should be opposite to that of the obliquely arranged fiber sets to avoid changing the direction of the fibers. The above-mentioned exposed fiber part is covered by the newly printed concrete, and overlaps with the subsequent printed fiber in the length direction to ensure the transmission of the bo...
Embodiment 3
[0061] Step 1. Use multiple print heads to realize that one of the print heads prints the flake layer of normal concrete, and the other print heads print fibers;
[0062] Step 2. If the amount of concrete extruded during printing is small, horizontal fiber printing can be arranged between layers; the most favorable way is to print horizontal fibers directly inside the concrete extrusion. This requires synchronous extrusion of horizontal continuous fibers in the direction of travel of the printing head when concrete is extruded, or even continuous iron wire.
[0063] Step 3. The fibers to be arranged are inserted into the printed concrete in a specific direction by the same print head according to the required arrangement position, according to the converted fiber amount, direction and position.
[0064] Step 4. The fiber is inserted into the printed concrete, and part of the length is reserved outside the layer.
[0065] Step 5. When printing the next layer of concrete, the r...
PUM
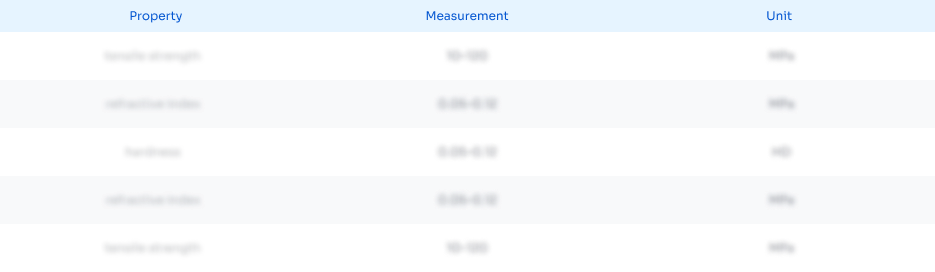
Abstract
Description
Claims
Application Information

- R&D
- Intellectual Property
- Life Sciences
- Materials
- Tech Scout
- Unparalleled Data Quality
- Higher Quality Content
- 60% Fewer Hallucinations
Browse by: Latest US Patents, China's latest patents, Technical Efficacy Thesaurus, Application Domain, Technology Topic, Popular Technical Reports.
© 2025 PatSnap. All rights reserved.Legal|Privacy policy|Modern Slavery Act Transparency Statement|Sitemap|About US| Contact US: help@patsnap.com