A latticed honeycomb beam segment and a large-span latticed steel beam and its fabrication and installation method
A lattice type, honeycomb beam technology, applied in the direction of joists, girders, trusses, etc., can solve the problems of increasing wind load on buildings, difficult to reflect economy and applicability, and unfavorable control of overall deformation of the structure. , to achieve the effect of expanding the applicable span, large rigidity and light weight of the structure
- Summary
- Abstract
- Description
- Claims
- Application Information
AI Technical Summary
Problems solved by technology
Method used
Image
Examples
Embodiment
[0039] Such as figure 1 As shown, the long-span lattice steel beam 1 in the illustration includes the mid-span lattice honeycomb beam section 2, the truss beam section 3 near the support and the transition section 4, and the lattice honeycomb beam section 2 and the two ends of the truss beam section 3 and the transition section 4 are rigidly connected, and the fulcrum of the large-span lattice steel beam is set at the lower chord node of the truss beam section 3 .
[0040] In this embodiment, the long-span lattice steel girder is welded with hot-rolled section steel, cold-formed thin-walled section steel or steel pipe to form a mid-span lattice type honeycomb beam section and a truss beam section near the support. and transition sections, each section is spliced on site to form a variable-height lattice steel beam with a zigzag or curved upper chord and a horizontal lower chord. The lattice honeycomb beam section includes upper chords, lower chords, vertical webs, and obliq...
PUM
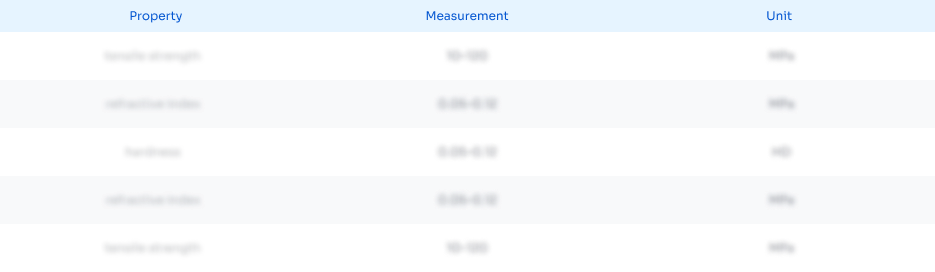
Abstract
Description
Claims
Application Information

- R&D
- Intellectual Property
- Life Sciences
- Materials
- Tech Scout
- Unparalleled Data Quality
- Higher Quality Content
- 60% Fewer Hallucinations
Browse by: Latest US Patents, China's latest patents, Technical Efficacy Thesaurus, Application Domain, Technology Topic, Popular Technical Reports.
© 2025 PatSnap. All rights reserved.Legal|Privacy policy|Modern Slavery Act Transparency Statement|Sitemap|About US| Contact US: help@patsnap.com