Cationic modified polyester/polyester one-bath process dyeing technology
A cationic, polyester technology, applied in the field of yarn and fabric dyeing process, can solve the problems of easily damaged products, unstable color, long process flow, etc., and achieve the effect of reducing pollution, shortening dyeing time, and shortening process flow
- Summary
- Abstract
- Description
- Claims
- Application Information
AI Technical Summary
Problems solved by technology
Method used
Image
Examples
Embodiment 1
[0019] Embodiment 1: yarn dyeing, cationic polyester / conventional polyester doubling
[0020] Raw materials: 70D / 72F conventional polyester and 75D / 72F high-temperature cationic modified polyester are paralleled.
[0021] Color: Cationic Modified Polyester Dark Blue, Regular Polyester Light Blue.
[0022] Same bath dyeing prescription:
[0023]
[0024] Process operation instructions: Put the raw materials to be dyed into the dyeing vat, enter the water to the specified amount, heat up to 25°C, add water-absorbing quick-drying agent, disperse leveling agent, and glacial acetic acid for 2 minutes → add disperse dyes and turn for 3 minutes → add precipitation preventive agent Rotate for 2 minutes → add cationic dye and transfer for 3 minutes → heat at 1°C / min to 78°C for 8 minutes → heat at 0.5°C / min to 98°C → heat at 1.5°C / min to 128°C for 50 minutes and then Cool down to below 80°C and drain→Wash with hot water→Add cationic soaping agent 1g / L for soaping at 70°C for 15 mi...
Embodiment 2
[0026] Example 2: Sports Seamless Vest Garment Dyeing
[0027] Raw materials: 70D / 72F conventional polyester accounted for 35.7%, 75D / 72F cationic modified polyester accounted for 38.3%, 50D / 24F cationic modified polyester accounted for 26%.
[0028] Product: Sports Vest
[0029] Color: dark red, light kenaf, cationic modified polyester dyed light red, conventional polyester deep red.
[0030] Same bath dyeing prescription:
[0031]
[0032] Process operation instructions: Put the raw materials to be dyed into the dyeing vat, enter the water to the specified amount, heat up to 30°C, add water-absorbing quick-drying agent, disperse leveling agent, and glacial acetic acid for 3 minutes → add disperse dyes and turn for 5 minutes → add precipitation preventive agent Rotate for 3 minutes → add cationic dye and transfer for 5 minutes → heat up to 80°C at 1.5°C / min and hold for 11 minutes → heat up to 100°C at 1°C / min → heat up to 130°C at 2°C / min and hold for 55 minutes Cool d...
Embodiment 3
[0034] Embodiment 3: two-color yarn dyeing
[0035] Raw materials: 70D / 72F conventional polyester and 75D / 72F high-temperature cationic modified polyester are paralleled.
[0036] Color: black fluorescent green two-color yarn
[0037] Same bath dyeing prescription:
[0038]
[0039] Process operation instructions: Put the raw materials to be dyed into the dyeing vat, enter the water to the specified amount, heat up to 35°C, add water-absorbing quick-drying agent, disperse leveling agent, and glacial acetic acid for 5 minutes → add disperse dyes and turn for 8 minutes → add precipitation preventive agent Rotate for 5 minutes → add cationic dye and transfer for 8 minutes → heat up to 82°C at 1.5°C / min and hold for 12 minutes → heat up to 102°C at 1°C / min → heat up to 132°C at 2°C / min and hold for 60 minutes Cool down to below 80°C and drain → hot water washing → add conventional soaping agent 1g / L, soda ash 2g / L at 80°C for 15 minutes → add cationic soaping agent 2g / L at 70...
PUM
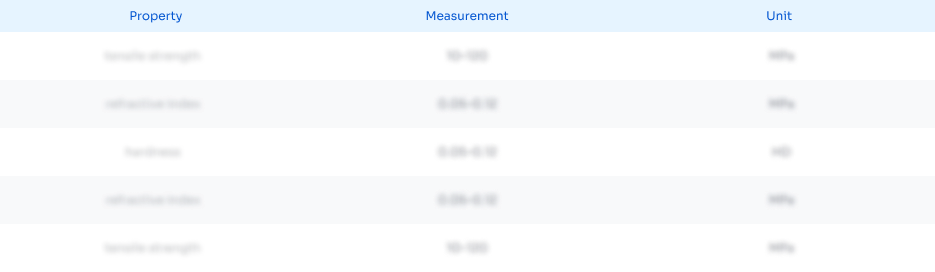
Abstract
Description
Claims
Application Information

- R&D
- Intellectual Property
- Life Sciences
- Materials
- Tech Scout
- Unparalleled Data Quality
- Higher Quality Content
- 60% Fewer Hallucinations
Browse by: Latest US Patents, China's latest patents, Technical Efficacy Thesaurus, Application Domain, Technology Topic, Popular Technical Reports.
© 2025 PatSnap. All rights reserved.Legal|Privacy policy|Modern Slavery Act Transparency Statement|Sitemap|About US| Contact US: help@patsnap.com