Hot metal pre-dephosphorization method
A technology of molten iron and pre-dephosphorization, which is applied in the field of pre-dephosphorization of molten iron, can solve the problems of high heat and low dephosphorization efficiency in the pre-dephosphorization process, and achieve the goal of reducing the production cost of the converter, increasing the metal yield, and increasing the carbon content at the end point Effect
- Summary
- Abstract
- Description
- Claims
- Application Information
AI Technical Summary
Problems solved by technology
Method used
Image
Examples
Embodiment Construction
[0025] Starting from the thermodynamic conditions of dephosphorization, the main points of dephosphorization control are determined as follows:
[0026] 1. Slag control
[0027] by attaching figure 2 CaO-2CaO·SiO 2 -CaF 2 The study of the ternary phase diagram established a reasonable dephosphorization slag system, and the composition of CaO was controlled at 30-60wt%, SiO 2 The composition is 10~40wt%, CaF 2 The composition is 5-30wt%.
[0028] 2. Temperature control
[0029] According to the thermal balance conditions of the dephosphorization process, the amount of slagging materials (lime, limestone, dolomite, fluorite, etc.) and coolant (ore, sinter, pellets, etc.) Large temperature fluctuations will cause splashing. It is recommended that the coolant feeding be controlled by PLC to ensure that the coolant feeding speed is balanced.
[0030] 3. Phosphorus and carbon content of semi-steel
[0031] The carbon content of the semi-steel is ≥3.4wt%, and the phosphorus ...
PUM
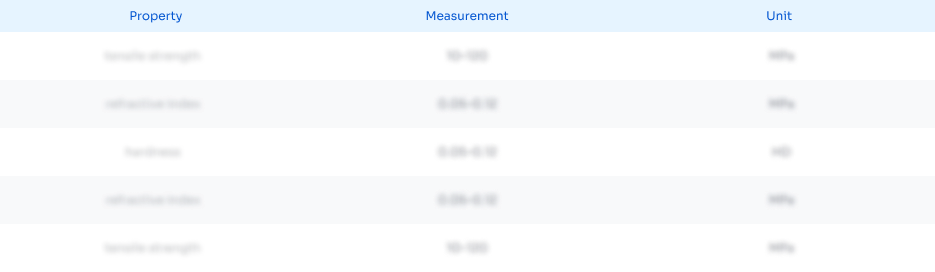
Abstract
Description
Claims
Application Information

- R&D Engineer
- R&D Manager
- IP Professional
- Industry Leading Data Capabilities
- Powerful AI technology
- Patent DNA Extraction
Browse by: Latest US Patents, China's latest patents, Technical Efficacy Thesaurus, Application Domain, Technology Topic, Popular Technical Reports.
© 2024 PatSnap. All rights reserved.Legal|Privacy policy|Modern Slavery Act Transparency Statement|Sitemap|About US| Contact US: help@patsnap.com