Heavy-load rolling linear guide-way pair capable of homogenizing errors
A technology of linear guide pair and guide rail, applied in the direction of linear motion bearings, shafts and bearings, bearings, etc., can solve the problems affecting the smoothness of slider motion, product performance damage, and uneven force on rollers.
- Summary
- Abstract
- Description
- Claims
- Application Information
AI Technical Summary
Problems solved by technology
Method used
Image
Examples
Embodiment Construction
[0027] combined with Figures 1 to 8 The specific embodiment of the present invention is described further:
[0028] A pair of heavy-duty rolling linear guide rails that can equalize errors, including a slider 4 and a guide rail 1. The slider is clamped in the guide rail and slides reciprocally along the guide rail. The two sides of the guide rail and the slider are respectively provided with four tracks. Contact surfaces. Rolling bodies 3 are arranged between the four track contact surfaces of the guide rail and the slider, and the rolling bodies move along the sliding direction of the slider; the two sides of the rolling bodies are smooth generatrixes, and the generatrixes include a force bearing in the middle The arc and the end of the corrected arc are corrected; the inner concave surface of the slider track forms an inner contact point with the generatrix of the rolling elements, and the outer convex surface of the guide rail forms an outer contact point with the generat...
PUM
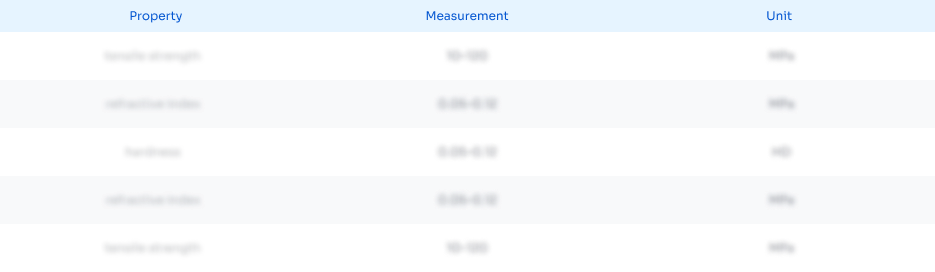
Abstract
Description
Claims
Application Information

- R&D
- Intellectual Property
- Life Sciences
- Materials
- Tech Scout
- Unparalleled Data Quality
- Higher Quality Content
- 60% Fewer Hallucinations
Browse by: Latest US Patents, China's latest patents, Technical Efficacy Thesaurus, Application Domain, Technology Topic, Popular Technical Reports.
© 2025 PatSnap. All rights reserved.Legal|Privacy policy|Modern Slavery Act Transparency Statement|Sitemap|About US| Contact US: help@patsnap.com